HISTORY OF
WELDING - IN THE BEGINNING
The Bible mentions Tubal
Cain, "forged all types of tools from bronze and iron." He may
have been one of the first to join metals with the forging process. His flame was
an open hearth into which he placed the metals to be heated to the forging
temperature. (Of interest, in forge
welding the material does not melt. It becomes very soft at temperatures
several hundred degrees lower. The most recent innovative joining process,
Friction Stir Welding, also does not
melt the base metal-it just becomes soft and plastic!)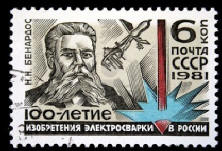
In 1881 a Russian inventor, Benardos demonstrated the
carbon electrode welding
process. An arc was formed between essentially a moderately consumable
carbon electrode and the work. A rod was added to provide needed extra
metal. An image of Nikolay Benardos is on a Russian stamp
honoring him as the "father of welding." A sketch of a carbon arc torch is
shown to his right.
|
In 1892 Morehead and Wilson accidentally discovered how to make acetylene.
It was found that combining acetylene with oxygen produced the hottest
known flame
temperature. Morehead (Photo Left)
went on to found one of the world’s leading chemical companies, Union
Carbide. In 1917 Union Carbide merged with the US owned Linde Air Products
company started by Carl von Linde in 1907 using his process of separating
air by liquefaction and distillation. The combination of acetylene and oxygen produced
a concentrated flame with a temperature of 5720 F, well above
the melting point of most metals allowing the oxyacetylene welding process
to develop into a leading metal joining technique. In addition to marketing
industrial gases in cylinders, Linde developed the
required regulators, torches and accessories needed for the oxyacetylene
welding and cutting process. The Linde Division became a pioneer in welding
research and innovations including an inventor and/or developer of many metal joining and cutting
processes including
Submerged Arc,
Heliarc, Plasma,
Electroslag
and MIG.
In 1904 Oscar Kjellberg in Sweden (Photo Right), the founder of ESAB, invented and
patented the covered electrode. This electric welding process made
excellent quality, strong welds very fast. ESAB became a world leading
enterprise supplying welding equipment, filler materials and welding
technology. They purchased AIRCO's electric welding
equipment business and in 1989 Linde's (subsequently renamed Praxair) former welding equipment
and filler metals business which had become a separate company, L-TEC. At
the same time they purchased the leading US innovator of flux cored wire and
low hydrogen stick electrodes, Alloy Rods.
In
1911, Lincoln Electric introduced the first variable voltage, single
operator, portable welding machine in the world. In 1914, James F. Lincoln
(Photo Left,) then President of the company, established the Employee
Advisory Board, which included elected representatives from every
department. His incentive management system helped Lincoln to become a
leading producer of electric welding equipment and filler materials.
They were instrumental in promoting welding as a reliable, cost effective
metal joining process
The unique
management techniques employed by Ji.F. Lincoln had an influence on the
development of welding history. A summary of some key points in his business book(s) and
some of my direct experiences related to the company is available as a PDF
download. The similarities to the management techniques employed by Henry Ford and Fred Taylor's
work are included. .Click for a Report Comparing J.F. Lincoln's Management Ideas with Those of Henry Ford, Both Supporting Fred Taylor's Concepts of Engineering Management
On November 16, 1916, a
supplier of industrial gases, the Air Reduction Company (AIRCO) was
officially formed and began producing and marketing high-purity oxygen and
other industrial gases including acetylene. This company introduced a number of innovations in the
welding industry, including
MIG Welding.
AIRCO sold their welding equipment business to ESAB in the 1980's, retaining
the very profitable industrial gas business. The AIRCO gas
business was
later purchased by the British Oxygen Company and in 2006 that enterprise
was purchased by Linde AG the German Company started by Carl von Linde. |
A significant invention was defined in a patent by Alexander.
He filed patent number 1,746,207 in
December 1924 for what came to be known as the
Atomic Hydrogen Welding Process.
It looks like MIG welding but hydrogen is used as the shielding gas which also
provides extra heat as it burns with the surround arc. |
A
major innovation was described in a patent
(US Patent number
2,043,960) that defines the Submerged Arc Process invented by Jones, Kennedy and Rothermund. This patent was filed
in October 1935 and
assigned to Linde Division of UCC. The
Specification states, Page 4, Column 2, Lines 4 through 7 that the application
was in part a continuation of applications Serial Numbers 657,836 and 705,893
filed in February 1933 and January 1934. The following was excerpted from
an article written by Bob Irving in
The Welding Journal; “The importance of welding was emphasized early in the war when President
Roosevelt sent a letter to Prime Minister Winston Churchill, who is said to have
read it aloud to the members of Britain's House of Commons. The letter read in
part, "Here there has been developed a welding technique (referring to
Submerged Arc Welding) which enables us to
construct standard merchant ships with a speed unequaled in the history of
merchant shipping." |
Russell
Meredith working at Northrop Aircraft Company in 1940 -1941 invented
the TIG process. This new
process was called "Heliarc" as it used an electric arc to melt the base
material and helium to shield the molten puddle. Mr. Jack Northrop's
dream was to build a magnesium airframe for a lighter, faster warplane and
his welding group invented the process and developed the first TIG torches.
The patents were sold to the Linde Division who developed a number of torches for different applications
and sold them under the brand name Heliarc.
Linde also developed procedures for using Argon which was more readily
available and less expensive than Helium.
|
In Welding Journal article Gus Manz interviewed one of the key
inventors of the MIG process (US Patent Number 2,504,868 -January 1949),
Glen Gibson. Mr. Gibson indicated he had observed the demonstration of
a manual submerged arc process by Lincoln Electric and had the vision to define
the process using and inert gas shield. He had been working on TIG welding
in the Development Lab at Airco at the time. He indicates although he went
on to be the owner of a very successful business; "..the greatest single
day in his life was the day Steve (Steve Sullivan worked with
Glen at the Lab) and I cranked up the first (MIG) welding gun."
|
On
July 26, 1955 Robert Gage (my old boss at the Linde Labs) filed US Patent
Number 2,806,124 for Plasma,
entitled "Arc Torch and Process." This
was the first Plasma Torch and Process patent. It had 29 claims and
was assigned to Linde. One of the patent figures is shown on the left.
Although usable for welding it has gained wide acceptance as the process
of choice for thermal cutting.
Bob Gage, photo right, was a
brilliant Physicist and a great boss. Although tough, he always made
you think, often with a critical statement such as; "Your solving a
problem not know to exist using a method known not to work!"
Bob managed Welding and Cutting R&D for the Linde Division
(in all US facilities) for many years.
See Brief History of
Plasma and Plasma Gouging Development
|
Other Inventions and More Details:
More information on the History of:
-
Submerged Arc
Welding (SAW)
-
TIG
Welding (GTAW)
-
MIG Welding (GMAW)
-
Electroslag Welding (ESW)
-
Friction Stir Welding (FSW)
can be found
at these links on our site (just click on the process)
|
Side Bar
J.F. Lincoln created a very
successful welding company employing many unique and creative management
techniques. Soon after he became General Manager in 1914 he
established an Employee Advisory Board and became President of the company
in 1928. He instituted an aggressive employee incentive system in 1934 and
"guaranteed employment" program in 1958. Lincoln Electric also
employed many unique business
philosophies related to pricing and selling. He wrote a book published
in 1961 entitled "A New Approach to Industrial Economics." Having just
reread this excellent text it has many suggestions and answers to the
current debates about rewarding hard work and employee/management trust
needed to keep America competitive.
During an Management
Masters program I wrote a report comparing Fred Taylor, considered the
father of scientific management, Henry Ford and James Lincoln. Taylor
defined the need to have individual incentives to reward hard work and Ford
and Lincoln successfully employed some of these principles. As with many good
ideas there is controversy and some of the best information about Taylor's
experiments and work are in the Congressional record of a year long probe in
1912 concerning his methods causing employees to "work too hard!"
Typical of Congress then and now, as a result of this Congressional probe it
passed a law saying no civil service employee could use a stop watch which
wasn't repealed until 1949!
The unique
management techniques employed by Ji.F. Lincoln had an influence on the
development of welding history. A summary of some key points in his business book(s) and
some of my direct experiences related to the company is available as a PDF
download. The similarities to the management techniques employed by Henry Ford and Fred Taylor's
work are included.
With our 2022/2023 (probably extending to 2024+) inflation, was reminded of the tough time for the welding equipment and filler metals business in the early 1980's. It was a struggle for all suppliers including Lincoln Electric, the US Market Leader. But for our company, the largest Industrial Gas Company in the US, it lead to divesting of the welding, cutting and welding materials business! Although a stressful time it was also challenging and fun as I look back. The following is an overview of how Linde's Welding & Cutting Business became L-TEC and was sold after 4 years to ESAB at double the purchase price. That provided the Investors triple their investment and the company that structured the Limited Partnership 25% of the gain. The report below shows how that was accomplished.
Competitive Capitalism Created Most Modern Welding Processes
CLICK PDF ICON TO Download 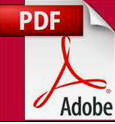
L-TEC_Investment_Triples_4_Years
CLICK to Download PDF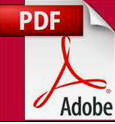
History-of-Welding-Distribution
CLICK to Download PDF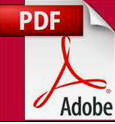
Lincoln, Ford, Taylor REVISED with addition of info from 2014 Book by Lincoln President Don Hastings
CLICK to Download PDF
Lincoln Electric received a lot of positive press from Harvard Business Review, etc. Some came from what was a unique business philosophy of focusing on being low cost producer, making the same products cheaper and lowering prices. But most came from paying hourly workers very high bonuses that in years past was 100% of earned salary and in the mid 1970's for some exceeded $100,000 total compensation. They also guaranteed a 30-hour work week in tough economic times.
However, that very ridged philosophy had flaws, and some are only coming to light in a Book from a former Lincoln CEO, Don Hastings! This paper gives an insight into how we competed with this low-cost producer, often using what the founder, JF Lincoln advised in his management books! Hope you find a fun read.
Click to Download PDF
|
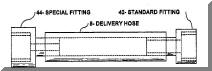
New innovations are still occurring in the welding industry. Our
recent inventions optimize MIG shielding gas flow at the weld start (US Patent
# 6,610,957; figure left. Patent numbers 7,015,412 and 7,019,248
are alternate approaches to solve the problem.) These devices reduce the
"Gas Blast" at weld starts by reducing excess stored gas over 80%
when welding stops. This significantly reduces gas waste which published
data shows typically exceeds over
60% of what is used! Reducing shielding gas waste typically saves a
MIG user 40 to 50% of total gas use while improving weld start quality. Our
Patent # 7,462,709 issued in 2008 and defines a device that allows most
flowmeters to be locked at the desired settings avoiding excess wasted gas.
Reducing waste
is very important in a competitive world environment.
|
In
2012 we were granted two patents related to helping a welders environment.
These patented welding helmets not only filter the air entering the helmet,
they simultaneously cool it, using a "thermoelectric cooling module."
Cooling the head helps cool the body. Excessive heat is a common
complaint of welders. These helmets help solve the excessive heat problem by
providing cooled, clean, breathable air.
We are searching
for a company to license these helmet designs, including fabricators that
employ a large number of welders who would benefit from the reduced heat and
a better working environment. Contact
Jerry_Uttrachi@NetWelding.com if interested. |
Have a MIG Welder?
Improve Weld Start Quality and
Have Shielding Gas Cylinder Last at Twice as Long!
Note: Our Patented
GSS
is Not Available in "Stores"
We Focus on Saving NOT
Selling Shielding Gas"
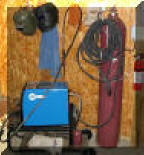
A home shop fabricator
in Georgia with a Miller TM 175 amp welder
purchased a 50 foot Gas Saver System (
GSS
TM
) so he could use a larger cylinder
and mount it on the wall of his shop. He wrote:
"The system works great.
Thanks for the professional service and
a great product."
Click To See His Home Shop
A Professional
Street Rod Builder Had This to Say:
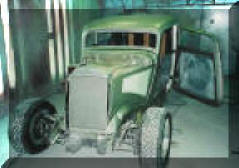
With their standard MIG welder gas delivery hose the peak shielding flow at
weld start was measured at 150 CFH. That caused air
to be sucked into the gas stream causing poor weld starts. With the replacing their existing
hose, the peak flow surge at the weld start was about 50 CFH. Total gas use
was cut in half.
Kyle Bond, President, quickly saw the improvement
achieved in weld start quality as a significant advantage! Kyle, an
excellent automotive painter, was well aware of the effects of gas surge
caused by pressure buildup in the delivery hose when stopped. He has to
deal with the visible effects in the air hose lines on the spray gun in his
paint booth! The paint surge is visible and creates defects unless the gun
is triggered off the part being painted! We can’t do that with our MIG gun!
GAS SAVER SYSTEM (GSS TM)
PURCHASE INFORMATION
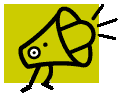
GSS
Customer Testimonial: PDF Download
|
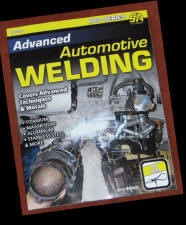 |
"Advanced Automotive Welding"
Author: Jerry Uttrachi
(President of WA Technology)
Book includes overview of all welding processes and welding science.
CLICK for Book Details |
Download
PDF Overview of the "Advanced Automotive Welding" Book with Contents Page. |
Book Review by a Race Car Builder:
Dear Jerry:
Thank you for the wonderful book that you wrote. The content is possibly
one of the best written and cogently assembled pieces of welding instruction
that I've ever read.
I have literally dozens of books on welding that span a good
5 or 6 decades. Some of the better ones were written back in the 40's for
training the wartime workers. It's amazing to me that it took over 60 years
for a book to be published that is comprehensive and comprehendible that
explains in everyday language, the latest techniques in the welding arts and
sciences. The coverage of the subject was more complete than I have ever
seen. This is a classic, and sure to be a benchmark reference book for years
to come.
I have recommended the book to my membership at the website
and continue to promote it wherever I go. I know that ADVANCED AUTOMOTIVE WELDING will be
a huge success, and we are honored to have been a small part of it. Please
don't hesitate to call if there is every anything that we can do for you.
Please feel free to use me as a reference or testimonial as
you see fit. Wishing you continued success.
Jim Harvey: HRE Fabrication, Levittown, NY 11756 |
The
"Gas Blast" at MIG Weld Start Causes Problems:
1)
Shielding Gas Waste
- typically 50% of gas used
2) Inferior Weld Quality
- due to air pulled in gas stream
See Patented
Gas Saver System (GSS)
Solution
GSS Works for TIG Welders with Foot
Pedal or Thumb Control
|
Stop
Wasting Shielding Gas!!
See YouTube Videos
Including Our Patented MIG Shielding
"Gas
Saver System" (GSS)
Science of MIG
Shielding Gas Flow Control
Why MIG Gas Waste
Detailed Review of GSS
Short Overview of GSS-90 Seconds
What User Say About
GSS
Welding Race Cars
Rat Rods-Then and Now
Welding: Go Green
|
▲HOME
►CONSULTING
SERVICES
|