|
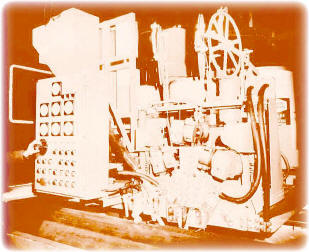
Page 1 of 5
HISTORY OF SUBMERGED ARC WELDING
One of the most significant welding processes invented and
widely employed throughout the world is Submerged Arc welding. Many of the
welded products which utilized this process contributed to significant changes
in the way we live, namely: |
- Large girders for modern long span bridges
- Massive beams needed for tall buildings
- Electric Power Generation:
- Penstocks to transport water from dams through water
turbines
- Steam boilers, piping, turbines
- Nuclear vessels
- Wind turbine towers, transmission towers
- Petrochemical vessels and piping
- Chemical processing vessels
- Ships and submarines
- Railroad cars and locomotives
- Large presses and machine bases
- Natural gas and oil pipelines
- Offshore drill rigs
- Large diameter water pipe
- Many other heavy plate structures
- Thinner material products such as water heaters and
propane tanks
- Hardfacing for steel mills, earthmoving equipment, mining,
etc.
|
SOURCES OF INFORMATION
Several publications have summarized the sequence of events
that led to the development of the Submerged Arc process. Not all are
accurate. Fortunately a search of the US patents and a book by R.D. Simonson can set the record straight. The writer also has the benefit of
knowing and working with some of the persons directly involved with the process
development. Documentation of the facts presented is given with patent numbers,
references and photographs. It is suggested students search the US Patent
Record using the patent numbers provided. It is available for patents
issued from 1790 free of charge on the Internet. Often other patents than
those mentioned can be obtained by looking at those sited in subsequent patents.
ALL PUBLICATION RIGHTS AND MATERIAL PRESENTED ARE THE SOLE
PROPERTY OF WA TECHNOLOGY, LLC, AND SHOULD NOT BE COPIED WITHOUT WRITTEN
PERMISSION.
ANYONE IS FREE TO MAKE ONE COPY FOR PERSONAL
USE. THIS CAN INCLUDE ONE PHOTOCOPY, ONE PRINTED COPY, AND ONE EMAIL COPY. THIS
INCLUDES USE BY A STUDENT FOR AN ACADEMIC PURPOSE.
|
THE
BEGINNING
Submerged
Arc was not the first automatic welding process. Patents dating in the early
1920’s describe automatic welding processes. As an example, US Patent number
1,676,985 by Haughton assigned to the General Electric Corporation was filed in
September 1925. [File dates rather than patent issue dates will be quoted as
these are the first record of an invention]. An insert of the drawing from
the patent is shown on the left. As noted it is an elaborate devise for
automatic welding with a continuous bare wire feed from a reel to the weld
zone. The unique feature defined in this patent is the use of oscillation of
the wire in the joint to be welded. However, as with a number of other machine
patents of the era, it was used with an open arc in air. Other references note
the welds from this simple process contained porosity and were not suitable for
many applications. One stated that even with an improved version of the open
arc in air process, a manual weld made with covered electrode (SMAW) would be
used inside a vessel to prevent leaks. Other automatic processes of the time
used coated rods where the coating was slit as the weld progressed to allow
current to be transferred at a fixed point from the work. As with open arc
processes weld current was limited and weld quality often poor.
|
ROBINOFF PATENT
The use of
open arc automatic processes provides an appreciation of why the Robinoff patent
was considered as an advancement. Although often quoted as the “invention” of Submerged Arc, a careful
review will show it was in fact not! The patent, number 1,782,316, was filed in
May of 1929. The patent Specification and even Figure 2 (show at left)
show
what amounts to a relatively small amount of flux (by Submerged Arc standards)
being applied in the joint. Further on Page 1, Lines 40 to 44 in the
Specification it states: “The groove is then filled with a powdered scale
(ferrous oxide) to make the flux magnetizable.” On page 2, on Lines 43 to 48 in
states; “…the welding current will flow …through the rod and will become
magnetized so as to attract the flux 9. Their final claim, number 8 states;
“...moving the metal electrode … and drawing an arc causing said flux to
melt...” As will be mentioned later, if this were truly
a Submerged Arc they
would have the same difficulty as the inventors, i.e. Kennedy et al in defining
if there was an arc and would have at least not mentioned the presence of one!
However no doubt since there could be questions raised in any patent
litigation, Linde purchased the rights to this patent as well as those that were
significant. R.D. Simonson, in his book
“The History of Welding” (reference 1) pages 140 and 141 states; “Then the
Western Pipe and Steel Company called (referring to Harry Kennedy) for help with its Robinoff welding
process. Kennedy’s notes indicate that the problem there was attacked through
the welding flux being used. It soon became apparent this was no minor problem,
but one which, if it could be solved, would lead to the development of a basic
new welding process. Simonson further states on page 141; “Thus when the
business relationship between Kennedy and the Western Pipe and Steel Company
became mutually unsatisfactory in the early thirties the way was open for the
Linde Air Products Company to enter the picture. Linde’s recognition of the
value of the process at this early stage led to its commercial introduction in
1935 as the “Unionmelt” process.”
|
Page
1
2
3
4
5(last)
Have a Welder?
Improve Weld Starts and Have Shielding Gas Cylinder Last at Least Twice as
Long!
Note: Our Patented
GSS
is Not Available in "Stores"
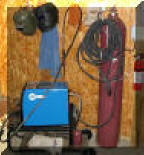
A home shop fabricator
in Georgia with a Miller TM 175 amp welder
purchased a 50 foot Gas Saver System ( GSSTM
) so he could use a larger cylinder
and mount it on the wall of his shop. He wrote:
"The system works great.
Thanks for the professional service and
a great product."
Click To See His Home Shop
A Professional
Street Rod Builder Had This to Say:
With their standard MIG welder gas delivery hose the peak shielding flow at
weld start was measured at 150 CFH. That caused air to be sucked into the
gas stream causing poor weld starts. With the
GSS replacing their existing hose, the peak flow surge at the
weld start was about 50 CFH. Total gas use was cut in half.
Kyle Bond, President, quickly saw the improvement achieved in weld start
quality as a significant advantage! Kyle, an excellent automotive painter,
was well aware of the effects of gas surge caused by pressure buildup in the
delivery hose when stopped. He has to deal with the visible effects in the
air hose lines on the spray gun in his paint booth! The paint surge is
visible and creates defects unless the gun is triggered off the part being
painted! We can’t do that with our MIG gun!
GSS
Customer Testimonial: PDF Download
See
Video Showing What Users Say About Our Gas
Saver System-CLICK
Here or Picture
▲HOME
►CONSULTING
SERVICES |
New
Info-"Friction Stir Welding"
|
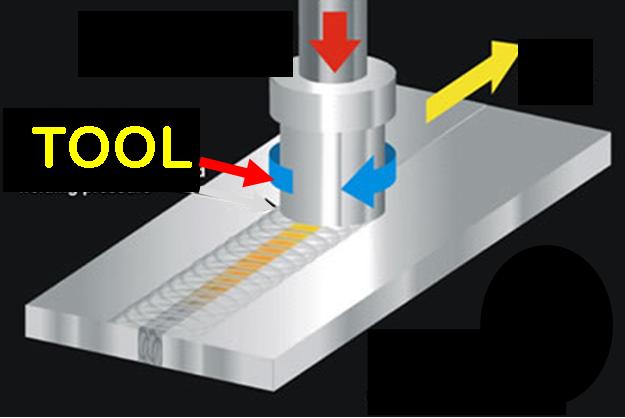 |
|