WELDING “HEAT TREATED” 4130
(QUENCHED
AND TEMPERED) Chrome Moly (Chromoly)
|
Pronouncing Chrome-Moly
I always pronounce it as Chrome-Moly. Not, cromoly, pronounced like two animals!
CLICK to SEE DETAILS: |
Video-Welding 4130
CrMoly
|
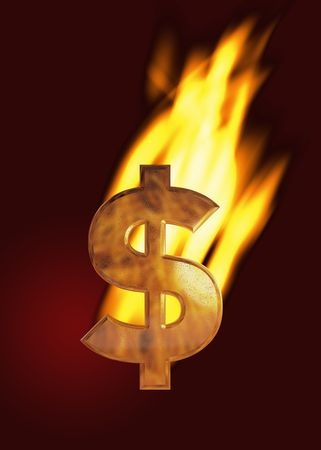
Alert !!
Argon Prices Have More than Doubled in Past Several Years!
Two European companies have bought key US Industrial Gas Companies, Airgas and Praxair. They now have 77% of the North American Argon production! Prices will go higher!
See a
Video
or Download a PDF Report showing why the price increase and the reason a
major Argon and Helium Producer and a leading Airplane
Manufacturer purchased 300 of our patented Gas Saver Systems for
their TIG Welders to cut gas use
up to half, by reducing waste! |
This
web page presents information about welding
heat treated,
high strength
4130 Chrome Moly tubing for race car frames where no post weld heat
treatment is utilized. We are not advocating this be done, in fact in
most cases just the opposite.
The reason for discouraging welding
heat treated, high
strength
4130 tubing without subsequent appropriate heat treatment
(meaning heating the finished weldment to 1600 F,
quenching in oil or water and then tempering to 1000 to 1150 F) is that the
area next to the weld will have much lower
strength and
may contain some brittle
areas!
We’re presenting this
information because of issues with:
-
AA Fuel Dragsters being allowed to use
higher strength, heat
treated 4130 and increased stresses for some frame members. (Cory McClenathan crashing at Bristol, Tenn. apparently
because of excessively thin wall frame tubes that
experienced local buckling at 300 mph!)
-
Some Funny Cars where Heat Treated
4130 apparently had been used and the chassis broke in what reportedly appears to be
a brittle manner.
-
Questions received in technical talks at
American Welding Society meetings and emailed to our Web Site from
race car and custom motorcycle frame builders wanting to use this higher
strength -"stiffer" material (when it is NOT stiffer!)
-
A recent article in a popular car
magazine which reinforced the need to define that increased “strength”
Does Not Mean “increased
stiffness!”
A Definitions Page is
provided to keep this discussion of reasonable length. Just click on the
words in
bold italics
to obtain a non
metallurgist definition.
Note: If your going to
"heat treat" the
finished welded 4130 part (by heating to 1600 F, quenching in
oil or water and then tempering to about 1100 F) see comments from my original Article published in
The American Welding
Societies Journal and quoted on this web site page. |
WHY 4130 IS STRONGER WHEN “HEAT TREATED”
Also, Why Recommended Welding Rod and
Procedures for Welding Normalized 4130 Cannot be Used to Solve the Problems
That Can Occur When Joining Heat Treated Material.
In the mid 1970’s, while managing a welding
shielding gas, MIG wire, TIG rod R&D Laboratory, I received a call from
a dragster chassis manufacturer requesting a recommended TIG rod for joining
normalized
4130. They did not plan to use preheat or any post weld
heat treatment. To minimize the chances of weld cracking when mixed with this
high carbon (by welding standards) 4130 material, a low carbon AWS ER70S-2 TIG rod
was recommended. This alloy rod has become widely
accepted as an excellent solution and has proven successful over many years. Welding
heat treated 4130
has totally different implications. The area next to the weld, not just the
weld metal, becomes the critical issue.
The
reference to
heat treated steel generally means the material is heated to a
temperature where a structural change occurs in the crystal lattice.
In the case of 4130 about 1600 degs F. At these temperatures the iron atoms have
a Faced Centered
cubic
arrangement (right in the figure above) and carbon atoms are interspersed between. If
cooled slowly, the atoms will rearrange to a low stressed
Body Centered
cubic
state (left in figure.) However if quickly
quenched
from 1600 F the structure does not realign to a
Body Centered
cubic structure but rather a
Body Centered
Tetragonal arrangement
(as noted in accompanying figure one side of the rectangle is shorter than
the other so it is not a cube) leaving a very
highly stressed material which is very
hard and strong. This
metallurgical structure is called
Martensite (named after metallurgist Adolf
Martens.) The resulting
tensile strength
could be in the range of 250,000 psi. Unfortunately it is
also very brittle.
What does brittle
mean? It means this very strong steel can act like glass when subjected
to a sharp blow or highly stressed environment! A positive term used to
quantify a steels resistance to brittle failure is a property called
toughness.
One measure of toughness is the Charpy test (although not useful for
very
thin material its valuable
to understand the
Charpy test.) The photo below left shows two broken Charpy test specimens.
The lower two matching pieces shows how
brittle
steel looks. There was little energy required to initiate and sustain the
fracture. The upper broken specimen shows the deformation that took place at
the outer edges and the matt finish in the center requiring more energy to
break the Charpy bar. To reduce this
brittleness, the quenched and hardened steel can be
tempered.
Tempering
requires reheating the very
quickly cooled steel to usually 700 to 1100 degs F. For gears and items
that need to be
hard, and that will operate at higher temperatures, a low tempering
temperature may provide enough
toughness.
However for 4130 used in structures, the
tempering
is usually done at about 1000 to 1100 degs. F to provide acceptable resistance
to brittle
failure. At these
tempering
temperatures a fully
quenched
and tempered
(Q&T) 4130 will have
strength of about 150,000 psi but will have higher
toughness
and ductility
than the as
quenched
material.
There is a
tempering temperature
range between 500 and 700 degrees where the steel may not improve
and may even reduce somewhat in toughness. This
reheat range should be avoided (see graph below.)
In the weld
Heat Affected Zone (HAZ) we can't avoid reheating the tubing from
a temperature close to the melting point of the steel, 2500 deg F, to temperatures in and below
that range which will decrease the strength! Tempered
properties are also dependent on
tempering time. The following table presents
the strength of 4130 after various heat treatments:
|

|
Note the
strength can be reduced after
heat treating
to 115 ksi (Note 1 ksi = 1000 psi) by
carefully reheating to 1200 F. The exact temperature and time are very
important. Heating with a torch can not assure the proper desired
properties.
The
graph left shows the resulting
toughness
after tempering to specific
temperatures. Note there is a low
tempering temperature
where the
toughness
does not increase and may actually
decrease.
CAUTION:
When welding
heat treated,
Q&T 4130 the area adjacent to the weld deposit (Heat Affected Zone)
will reduce in strength.
|
WELD HEAT
AFFECTED ZONE PROPERTIES
Weld metal chemistry can be controlled by
the type of welding filler rod/wire used. The amount of base material melted into the weld
deposit must also be
considered. When very small fillet welds are made in 4130 tubing the
large amount of melted high carbon (by welding standards) base material in the
weld deposit can significantly increase weld
strength. That is why we
recommended AWS ER70S-2 when welding normalized
4130. It has very low,
0.06 carbon so when mixed with the 0.33 carbon in the 4130 the weld deposit carbon content is at a
lower level, less susceptible to
cracking.
Where the melted weld properties are
influenced by the rod/wire selection, they have no influence in the area next to the weld called the
Heat Affected Zone (HAZ.) In the photo left, the
weld and
HAZ are revealed by chemical
“etching” a cross section. The outer etching boundary is
defined as a line that reached about 1300 degrees F. The line exists
because a metallurgical change occurs in steel at that temperature. Therefore
the visible
HAZ was
heated to a temperature from about the melting point of the steel (about
2500 degs F) next to the weld through this 1300 deg F line then on to 500 F
and lower. The width of the
HAZ area will be
larger when welding thinner materials. If
previously
quenched
4130 is
tempered
to 1050 degs F to
achieve the desired properties, we have essentially
tempered
the tubing next to the weld from 2500 degs F all the way down to the 1050
degs F! The time
at temperature is also a factor and will depend on weld heat input, wall thickness etc. In
general, the
HAZ will have a
strength much less than the “after tempering” 150,000
psi, for example! In fact that area will probably be no stronger than if we welded the more
typically used normalized
4130 tubing.
Normalized 4130 tubing was cooled more slowly from a high temperature,
never creating the
hard, brittle
Martensitic
structure and it is also much tougher
than the as-quenched
material.
Normalized 4130
usually has a
strength
of about 95,000 psi.
The mixture of metallurgical structures present in the
HAZ of welded
Q&T
4130 may contain some
brittle areas.
|
WHAT HAPPENS WHEN WELDED Q&T 4130 IS STRESSED?
When the structure is stressed, the
~150,000 psi
strength
tubing material will
have a much weaker (perhaps 90,000 psi)
HAZ area between
the joined pieces.
The strength will be reduced in the
HAZ in a band heated from the 2500
degs F area next to the weld all the
way down to a band that reaches the 1050 degs F
tempering
temperature. That weakened band could be wide in
deposits made in thin wall tubing as shown in the photo right.
Note the area that reached 1000 deg F is further away from the weld than the
visible 1300 F outer etching bounder. It addition, if any brittle
metallurgical constituent exists, cracks may form and propagate in the
highly stressed HAZ even at
lower overall stress levels. Because of the lower strength in the
HAZ our usual suggestion
(which has proven successful for many years) of using an very ductile AWS ER70S-2
welding rod and making slightly larger fillets to compensate for the somewhat lower
strength
will not help a weak (with some potentially brittle areas) HAZ!
|

An interesting way to see what temperatures are reached when
a weld was made is on a sand blasted surface is shown in the above
photo. Steel oxidizes to specific colors depending on the temperature
reached. These are called temper colors. This photo shows how far from the weld
the plate reached 500 F while welding.
|
STIFFNESS
Why use “high
strength”
4130 in the first place? All else being equal 250,000 psi oil/water
quenched
4130 tubing is no ”stiffer” then mild steel with 50,000 psi
tensile
strength! Both will bend the same amount when loaded (assuming the
structure does not take a permanent set or what is referred to as yield.) This assumes the same tubing
diameter and thickness are being compared. Generally when switching from a lower strength
material, for example mild steel at 50,000 psi to 4130 at 95,000 psi tensile
strength, a different size tube will be employed. Refer to the web page
of properties and metallurgical definitions under the section on
stiffness, to understand what needs to be done to achieve
a “stiffer” structure. 4130 Chrome Moly is also the same weight
per cubic inch as mild steel. The only way it can be stiffer and lighter is to use large diameter tubing with a thinner wall thickness.
SUGGESTIONS
What Should be Done to Join Heat Treated
4130?
First be sure it is understood why the
higher strength
is being used. If there is a real structural benefit or are you just
getting into and area where
local buckling
may occur? If the extra
strength is a real benefit, then perhaps welds can be
placed in an area of lower stress. Other joining techniques can also be
considered. Racing bicycle manufactures use special brackets or "Lugs" that capture
the tubing and then they braze the joints at much lower temperatures than
caused by welding. You could
also heat treat the final product. It is very difficult to take a
complex fabricated chassis, heat the assembly (with the needed fixture
to minimize distortion) to 1600 deg F, then quench in
oil and have it remain in the desired shape! However one Baja race car team
reports they were going to do just that. Not sure how they managed the inevitable
distortion or if it was a successful approach!
|
SIDE BAR
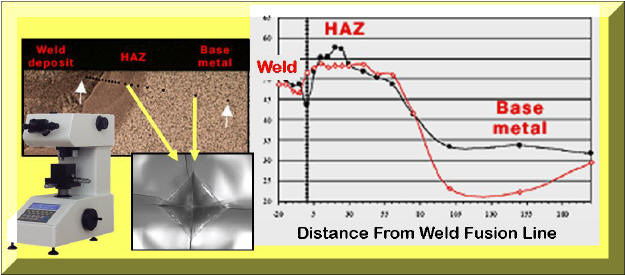
An interesting
analysis was developed from information presented on Metallurgical
Technologies' web site. They examined a weld made in 4140 steel which has
0.40 carbon. This steel is more hardenenable than 4130 meaning at
typical TIG welding cooling rates it can produce 100% hard, brittle Martensite in
parts of the HAZ. This is what appears to have occurred in this weld.
Two microhardness traverses of the Weld, HAZ and Base Metal are presented in the above graph
(typically these are taken near the top and center of a welded section.).
Converting the hardness data shown on the black line to approximate tensile strength; the unaffected Base Metal was ~150 ksi tensile
strength and the weld much harder with a equitant tensile of ~240 ksi.
The HAZ next to the weld had a hardness equivalent to ~300 ksi.
The base material may have been quenched and then tempered to about 1100 F to
achieve 150 ksi tensile strength. Mechanical property data for 150 ksi
Q&T
4140 shows it may have a reasonable Charpy toughness of ~60 ft-lbs. When
tempered to only 400 F it will have a tensile of ~260 ksi and only a brittle,
10 ft-lbs Charpy impact toughness. The ~300 ksi HAZ toughness would be even lower -"glass like!" In addition, the
hardness traverse shown on
the red line indicates a dip in strength to the equivalent of 110 ksi.
This probably occurred in an area that was subjected to a slower cooling
rate and reached a temperature above the original tempering temperature. To
reduce the HAZ strength and improve ductility in this 4140 weld, a minimum
preheat of 400 F or higher should be used even for thin material to
lower the cooling rates sufficiently to avoid the formation of Martensite.
Note, 4140 steel is
about twice as hardenable as 4130. This means a weld cooling rate that
is sufficiently slow to just avoid producing Martensite in a 4130 HAZ can
produce a 100% Martensitic structure in the HAZ of 4140 steel (See
Note Below.) With its lower,
0.30 carbon 4130 is less likely to have a brittle HAZ but if welding
heat treated, higher strength 4130 the HAZ will decrease in strength. Although 4130
presents
less of a HAZ problem then 4140 when welding Normalized material, if welding higher strength, heat treated
4130 a hardness traverse will define the approximate amount of strength
reduction and is
a method to evaluate weld procedures and HAZ properties.
The weld macro
section shown on the left of the above figure is not from their web site but
shows how a hardness traverse is made. A hardness testing device
incorporating a microscope (one type shown in white) is used employing a small
diamond indenter. The small black dots in the polished cross
section (seen between the white arrows) are the very small indentations made
with the hardness tester.
The magnified photo at the bottom shows their shape. The depth of the
indent with a fixed load is a measurement of hardness.
My recommendation is to have some
testing done by a competent metallurgical or welding research firm to
evaluate the quality of weldments in 4130.
With the amount of sponsor money spent on most racing series they surely can
be called upon to assist with researching weld quality and materials suitability
issues.

Email
for recommendations on hiring a firm.
Note:
As seen in a Continuous Cooling Diagram of 4130
(Click to See)
the nose of the graph is very close to TIG weld cooling rates in thin
material. With cooling rates that reach 900 F after about 5 seconds
little if any Martensite will be produced. With 4140 the nose of the
curve will be displaced
right to about 9 seconds. Even the slower TIG weld cooling rate shown
will produce Martensite in the HAZ. The cooling rate curves were
obtained using equations from the AWS Handbook; See
Calculations. |
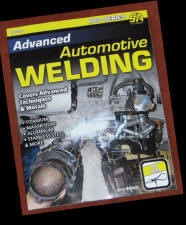 |
"Advanced Automotive Welding"
Author: Jerry Uttrachi
(President of WA Technology)
This 176 page book includes detailed metallurgical information about
welding Chrome-Moly
CLICK for Book Details |
If higher strength
steel is felt necessary why not use an alloy that is strong, tough and more readily weldable like HY-130.
For More Information on Welding 4130
Chrome Moly:
Click for BASIC 4130 WELDING
DETAILS
Click for
TECHNICAL & METALLURGICAL DETAILS
Click for
EQUATIONS
Defining Weld Cooling Rate in Tubing
Click for
METALLURGICAL DEFINITIONS
Click for
DEFINING "EFFECTIVE HEAT INPUT"
Click for WELDING A BETTER
STEEL; HY 130 |
Improve Weld Starts
and Save Money by Eliminating The
"Gas Blast" at MIG Weld Starts That Causes:
1)
Inferior Weld Quality and Excess Spatter
- due to the air pulled into the gas stream
2)
Shielding Gas Waste
- typically 50% of gas used
See Patented
Gas Saver System (GSS)
Solution
GSS
Works for TIG Welders with Foot Pedal or Thumb Control
|
Stop
Wasting Shielding Gas!!
See YouTube Videos
Including Our Patented MIG Shielding
"Gas
Saver System" (GSS)
Why MIG Gas Waste
Detailed Review of GSS
Short Overview of GSS-90 Seconds
What User Say About
GSS
Welding Race Cars
Rat Rods-Then and Now
Welding: Go Green
Engineering A
Pro Street / Street Rod
|
|
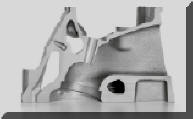
MIG Gas Delivery and the Small Block Chevy
Evolved in a Similar Way and Time!
Both had Advances and
Setbacks Before
They Were Optimized!
Click
for a PDF Report on the Similarities |

Free Technical Paper, "MIG
SHIELDING GAS
CONTROL"
CLICK ICON for PDF DOWNLOAD |
Thanks to those "Car Crazy" folks who have purchased
the Gas Saver System and commented on the improved starts and reduced gas usage
they have achieved. Many purchased our 6 foot prefitted
GSS,
Part Number WAT FB6,
a 3 or 4 foot system, FB3 or FB4 are also available.
GSS
Customer Testimonial: PDF Download
ONE PAGE SUMMARY
PURCHASE
PRODUCT

FREE Corvette Accessory Installation Info
|
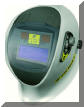
"WARNING: "Weld
Safely"
|
|