Video-Welding 4130
CrMoly |
Math Used to Generate 4130
Information. |
The Information Below;
 | Provides the math equations that estimate
the theoretical
cooling rates for TIG welds in thin wall 4130 tubes. |
 | The cooling rate equations were obtained from the Welding Handbook,
Volume 1, 9th Edition, page 100. |
 | Both thick and thin plate equations were developed by Professor C.A.
Adams et al.
|
|
The data is presented in a way so one can see the numbers
from each part of the equation. As the thickness was increased so was the
heat input. A TIG process efficiency of 0.5 (50%) was used which is
somewhat
higher than the sited Welding Handbook reference but errors on the side of
predicting a slower cooling rate. The thin plate equation is for two
dimensional heat flow and may be OK for a butt weld but a Tee fillet weld
will have faster cooling rate. Therefore despite trying to error on the side
of predicting slower cooling rates, they are all around the 1/4 in Jominy
bar location. The exact cooling rate will be somewhat dependent on the diameter of
the tube as well. However I would expect that perhaps 1/2 way around the
joint the cooling rate would be similar to that predicted. As the complete
circular weld is made the last part will have a preheat from the weld start.
However if a brittle structure is formed in any area and a crack forms, that
is sufficient to be a problem. |
Equation Elements and Values
 |
Rc = Cooling rate
at weld centerline; deg F/min |
 |
k = Thermal Conductivity of
metal; BTU/min in deg F |
 |
p = Density of metal; lb/in3 |
 |
C = Specific Heat of metal;
BTU/ (lb deg F) |
 |
h = thickness of metal; in |
 |
Hnet = Net heat
input; BTU/in [V*I / ipm*.057*process efficiency] |
 |
Tc = Temperature
which cooling rate is calculated; deg F |
 |
To = Initial
plate temperature; deg F |
Welding Cooling Equations from
page 100 Welding Handbook Volume 1, 9th Edition |
Thick Plate Equation =Rc =-[2*3.1416*k(Tc-To)2]
/ Hnet |
Thin Plate Equation = Rc =
2*3.1416*kpC (h/Hnet)2(Tc-To)3 |
Calculate estimated cooling
rate @ 1100 deg F for thin wall 4130 tube welds:
Tube = .040 in wall; V (volts)
= 10; I (amps) = 70; travel = 12 ipm
Using thin plate equation:
 | -2*3.1416*0.024*0.29*0.11= -.00481 |
 | Hnet = 1.66 |
 | (h/Hnet)2 = 0.000579 |
 | (Tc-To)3 = 1.07*109 |
 | Rc = -2981 deg F / min = - 50 deg F / sec |
|
Tube = .0625 in wall; V (volts) = 10; I
(amps) = 90; travel = 11 ipm
Using thin plate equation:
 | -2*3.1416*0.024*0.29*0.11= -.00481 |
 | Hnet = 2.33 |
 | (h/Hnet)2 = 0.000718 |
 | (Tc-To)3 = 1.07*109 |
 | Rc = -3700 deg F / min = - 62 deg F / sec |
|
Tube = .093 in wall; V (volts) = 10; I
(amps) = 110; travel = 9 ipm
Using thin plate equation:
 | -2*3.1416*0.024*0.29*0.11= -.00481 |
 | Hnet = 3.48 |
 | (h/Hnet)2 = 0.000713 |
 | (Tc-To)3 = 1.07*109 |
 | Rc = -3671 deg F / min = - 61 deg F / sec |
|
REFERENCES USED;
 | US Steel Atlas of Isothermal Transformation Diagrams |
 | Republic Alloy steels |
 | R. A. Grange and Kiefer; "Transformation of Austenite on Continuous
Cooling and Relation to Transformation at Constant Temperature." |
 | Walter Crafts and John Lamont; "Hardenability and Steel Selection." |
 | AWS Welding Handbook; Volume 1, 9th Addition |
|
The
"Gas Blast" at MIG Weld Starts Causes Problems:
1)
Shielding Gas Waste
- typically over half the gas used
2) Inferior Weld Quality
- due to air pulled in gas stream
See Patented
Gas Saver System (GSSTM)
Solution That Costs Less Than a Refill.
GSS
Works for TIG Welders with Foot Pedal or Thumb Control
|
If a Search Engine Found This Page 1st- - - We'd Suggest
a Visit to The Basic Welding 4130 Page; Then Return. Click
Here This page presents the equations that support
the data in the 4130 Technical Details page.
|
ONE PAGE SUMMARY
PURCHASE
GSS PRODUCT
FREE Corvette Accessory Installation Info
Check Out Welding
Math Site
|
This Page Presents Welding 4130 Math, for
Other Information:
Click for BASIC 4130 WELDING
DETAILS
Click for
TECHNICAL & METALLURGICAL DETAILS
Click for
EQUATIONS
defining weld cooling rate in tubing
Click for
WELDING HEAT TREATED 4130 CHROME MOLY
Click for
METALLURGICAL DEFINITIONS
Click for WELDING A BETTER
STEEL; HY 130 |
Stop
Wasting Shielding Gas!!
See YouTube Videos
Including Our Patented MIG Shielding
"Gas
Saver System" (GSS)
Why MIG Gas Waste
Detailed Review of GSS
Short Overview of GSS-90 Seconds
What User Say About
GSS
Welding Race Cars
Rat Rods-Then and Now
Welding: Go Green
Engineering A
Pro Street / Street Rod
|
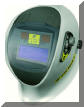
"WARNING: "Weld
Safely"
|