Welding Carbon Steel Chassis for NASCAR
etc.
By
JERRY UTTRACHI
Race cars require hundreds of
welds. Most welds join intersecting tubes that make up the frame and the all-
important roll cage. NASCAR chassis are unique in racing circles. The cars have
a minimum weight of 1542 kg (3400 lb), quite heavy by race car standards. NASCAR
requires the frame and roll cage components be fabricated from mild steel. This
allows the car to absorb the forces of a crash in a bend-before-break mode.
Although the driver cannot be protected from every incident, considering the
number of high-speed crashes encountered in NASCAR races, the drivers most often
walk away unhurt. This is a tribute to the chassis design and the weld quality.
In addition to the main chassis members,
some welds are made in 4130 chrome moly (molybdenum) tubing used for such things
as radiator supports. Suspension and steering components must also be welded.
Using the proper welding process and filler metals is very important to ensure
superior quality.
ESAB Welding and Cutting
Products, Florence, S.C., recently provided welding training to Petty
Enterprises at its Level Cross, S.C., facility. Below are some key points Bob
Bitzky (shown in photo), an ESAB welding engineer with 25 years of experience in
the welding industry, outlined for the team fabricators.
Pick the Process
The first consideration for mild steel welding, which is the predominant
material joined, is deciding what welding process to use. Shielded metal arc (SMAW,
also know as "Stick Welding"), gas tungsten arc (GTAW; also known as TIG or
HeliarcR, or gas metal arc (GMAW; also known as
MIG) welding are the three processes usually considered. Shielded metal arc
welding offers few benefits for in-shop use. The process presents slag removal
and possible slag entrapment issues. Gas tungsten arc welding can produce
excellent quality welds but so can gas metal arc welding. For the majority of
the fillet welds required, GMAW welding is faster and may produce less heat input
for lower distortion. This process also makes it easier to produce
consistent-quality welds. There is a misconception in the race car and street
rod circles that GMAW welding is not usable for critical welds. In fact, the GMAW
process is used extensively in industry to make very high-quality, critical
welds in items such as submarine hulls. Submarine hulls are made from
high-strength steel and are predominantly welded with the GMAW process. Pulsed
gas metal arc welding (GMAW-P) can provide welds without any spatter, similar to
GTA welding, as well as a controllable, hot arc to ensure the weld is fused to
the base metal. Short circuit GMAW welding (GMAW-S) is most often used on thinner
materials such as tubing and provides excellent quality in the hands of a
skilled welder.
Select the Proper
Filler Metals
Selecting the proper filler metal requires an understanding of the mechanical
properties desired and weld appearance considerations. Table 1 presents the
chemical composition of typical mild steel tubing and several welding wires that
can be used to join it.
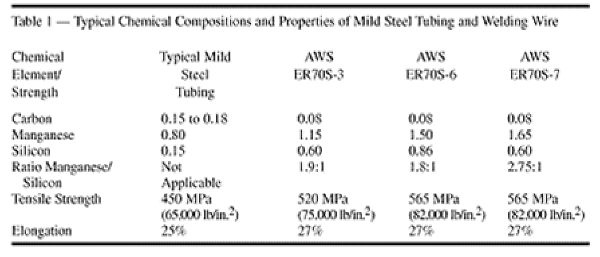
As seen in the table, to achieve the
required strength, welding wires contain less carbon than the base material and
more of the alloying elements, manganese and silicon. These differences, and low
levels of impurities in the welding wire, help provide crack-free and
porosity-free welds. Note that the manganese-to-silicon ratio in ER70S-7 is
significantly higher than ER70S-3 or ER70S-6. This higher ratio gives weld bead
wetting and makes it easier to produce undercut-free welds. ER 70S-7 is the
preferred alloy for welding mild steel. As noted, in general, the welds will be
at least as strong as the mild steel tubing.
Maintaining Welding Parameters
After selecting the welding process and filler metal, the proper welding
parameters must be maintained. Wire feed speed, voltage, and travel speed are
the key parameters to set and maintain. Welding current is a dependent variable
and is controlled by wire feed speed and electrode extension. This extension is
a critical variable. This is the distance from the end of the welding gun
contact tip to the workpiece. In tight confines, it may be desirable to use a
longer contact tip to ensure this value does not exceed about 1/2 in. If the
electrode extension becomes excessive, welding current will automatically
reduce, resulting in a colder weld with reduced penetration into the base metal.
It is important to keep the arc on
the leading edge
of the weld pool to assure proper tie-in to the base material.
[Although not as common when welding mild steel race car
chassis, making too small and too concave
fillet welds can create problems. This is especially true when using the
TIG (or GTA) welding process. CLICK HERE to see the information and
explanation of this picture in "Welding 4130" .]
Special Cases
Problems encountered can often be fixed. For example, a small weld made on a
heavy steel part cracked immediately after welding. The cause was attributed to
the very high restraint being placed on the small weld bead. Also, a
high-strength stainless steel alloy was used as the filler metal, which further
stressed the weld joint. The solution was to use a lower strength carbon steel
filler metal and a larger, more convex weld bead.
In another case, a crack occurred when
welding on a small threaded part. A chemical analysis performed on the part
indicated it was made from free-machining steel. This particular alloy used a
high sulfur content to aid the machinability. Some free-machine alloys also use
additions of lead or phosphorous. High sulfur, phosphorous, or lead additions
can only lead to poor quality welds. The solution for this application is simply
to not weld free-machining steels. The machine shop should pick another alloy.
Summary
Selecting the proper process is the first task of ensuring quality welds. Gas
metal arc welding can be used very effectively to achieve the desired results.
Picking the proper filler metal is also critical. An AWS ER70S-7 welding wire is
a good choice for welding mild steel.
For GMAW, selecting and
maintaining the proper welding voltage, wire feed speed, and electrode extension
are very important to achieving quality welds. The resulting welds should be
checked and verified to be sure they meet the requirements. As a minimum, all
should be checked and verified to be sure they meet the requirements. As a
minimum, all welds should be visually inspected for
undercut and smooth transition to base metal. When satisfactory welds are
produced, record the machine settings for future reference.
Closing Advice
Be sure to employ the skills of a qualified
welder. Quality Short Circuiting MIG welding requires keeping the arc in
front of the weld puddle to avoid lack of fusion or what is often referred to as
"Cold Laps." The weld may look OK on top but not be adequately fused to
the base material.
Small 110 volt input MIG welders may not have
sufficient power or the proper arc characteristics to assure quality welds when
making critical joints on material as heavy as structural tubing.
See a Video of Richard Petty and myself discussing
the importance of welding in keeping a driver safe!! Click here or on the move
camera ICON
What about Welding 4130? (see summary
elsewhere on this web site)