We've invented and patented a simple, inexpensive product that reduces MIG and TIG shielding gas use typically 40 to 50%, by eliminating waste while improving weld start quality!
A trailer manufacturer faced reducing production by 30% because of Argon allocation or purchasing our Gas Saver System (GSS )! They purchased 100 GSS's!
Over 15,000 Gas Saver Systems (GSS ) are in use at industrial fabricators Click to See Partial User List.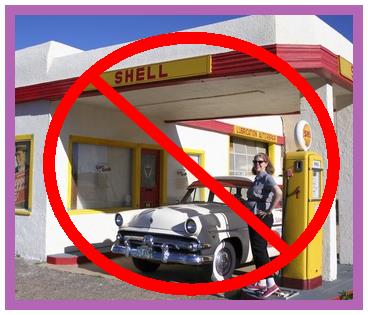
Our focus is helping fabricators reduce gas waste; NOT selling shielding gases. Therefore our Patented Products are Sold Directly -"Not In Stores!"
For Example Chart Industries has over 2500 GSS's installed in 7 US plants including China and the Czech Republic!
A Caterpillar Tractor plant recently reported improved starts with less internal porosity achieved with Gas Saver Systems (GSS) installed on all their MIG welders. Savings in rework costs as important than the substantial shielding gas waste reduction!
See Case 2 Showing Details of Similar Reported Improved Starts
Download a FREE PDF of 7 Testimonials of Weld Start Improvement with of GSS
It's simple to install and has no moving parts to wear of adjust! Just replace the existing gas delivery hose from gas source to welder, wire feeder or welding robot. Most large fabricators purchase product as bulk custom extruded hose and fittings and assembly their own as they replace existing gas hose. Email for prices, terms and payment options. Or ask about the simple way you can quantify gas leaks in cubic feet per hour and make quick simple measurements periodically to assure leaks are kept at an absolute minimum.
Email: Jerry_Uttrachi@NetWelding.com
GSS (photo
left) has been tested for gas savings by many of our
customers. It is a custom extruded small ID, large OD, fiber reinforced gas
delivery hose incorporating a peak flow limiting orifice. The GSS simply replaces the existing gas delivery hose between the gas
supply (cylinder or pipeline) flow control and the welder/wire feeder or welding robot. Steady state
flow rate is set with existing flow controls. The GSS has no moving parts to wear or knobs to set.
One fabricator found they were able
to produce 236 parts using a full cylinder of gas with their standard gas
delivery hose. With no other changes than installing our
GSS, they welded 632 parts with a full
cylinder! That is a 63% gas savings. A welding school recently found
similar savings. On average, fabricators who conduct gas use tests,
report total gas savings of 40 to 50%. The patented
GSS also limits peak flow at weld
starts to a maximum flow rate that avoids turbulence, providing better
weld start quality. Although reducing gas surge by 80 to 85%, unlike some other devices, it supplies sufficient extra shielding to purge air from the weld start area. We have a number of reported examples of welders
appreciating the weld start benefits. 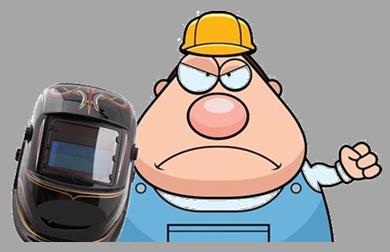
Don't confuse our patented GSS with past devices that justfrustratedwelders and/or managers! Welders appreciate the improved starts our GSS provides, while managers enjoy the gas cost savings!
See Why Feeder Mounted Orifices
Do Not Work to Reduce Gas Waste
See What Problems Occur if Low Pressure Devices are Used to Reduce Surge
Note, if purchasing for a number of welders, our custom extruded hose
is available on bulk reels and our custom hose fittings are available in pairs. Purchasing in bulk provides a
cost reduction from the fitted hose prices and is easier for installation with varying length and longer hoses (we have customers with 50 and 100 foot long systems.)
A 2nd Patented Gas Saving Product Available, a Flow Rate Limiter and Lock
After visiting many shops using flowmeters, a common problem
observed was excess flow rates being set by welders. We invented
and patented a "Flow Rate Limiter and Lock" (FRLL)
that fits over the flow control knob on most US made
flowmeters and prevents increasing flow. It does not alter the
flowmeter, it just clamps and locks onto the flow control knob with a set screw and is
easily installed.
FRLL Purchase Details: Click for Web
Page. |