The following are some formula for calculating the area of additional shapes we’ll use
to define weld
volume in a joint:
For the Triangle on the right: Area = B * H / 2
Note it is
like calculating the Area of a Rectangle and dividing by
2.
This
formula works for
any size and shape Triangle. Look at the Triangle below
left. Below right are picture examples that help show why this
equation works for any shape Triangle:
By
duplicating the Blue Triangle and rearranging pieces we can construct a
rectangle:
Referring to the three pictures on the
right:
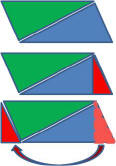
1) In the
top picture the Blue Triangle is copied and turned upside down
It is shown in Green.
2) In the
middle
picture we make a small Red Triangle to create a straight
perpendicular side on the Blue Triangle.
3) In the
bottom picture the Red Triangle is moved to the left side making a
straight side on the Green Triangle.
4) That makes a Rectangle with one
side still equal to B and the other H.
5) The AREA as defined for a
Rectangle is B * H.
But remember we duplicated the Blue Triangle so to get the AREA
of the Original Blue Triangle we have to divide by 2 hence
the formula: Area = B * H / 2
Area of a
Segment (Weld Reinforcement)
This
is one Area that is
often used in calculating weld metal area and
volume; it is called the area of a Circle Segment and shown in Red
on the photo left. This is what is used to calculate the area of
Weld Reinforcement. The accurate way to do this is to calculate the area of a
segment of Radius R (that is the combined Green and Red Areas;) use
the length of the Cord W (width of weld) and subtract the area of the
triangle formed by the Cord and distance from the Center of
the Circle and the Cord (the Green Area.) This leaves the Area between the
Cord and the Outer Area of the Circle (Red Area) or Weld Reinforcement
in our case.
However we
would have to estimate the Radius of the circle making the
reinforcement and the angle of that Segment. Not an easy item to
estimate. Since we know the weld bead height (or the desired maximum height
by code, usually 3/32 or 1/8 inch) and the weld height is much smaller than
the weld width we can use a method that estimates the area and is
probably
better than estimating the radius. The formula is:
Approximate Area of a Segment (Weld Reinforcement) = (2 H * W) / 3 + H 2 / 2W
Since weld reinforcement is not a
perfect circle, the value obtained is sufficiently accurate for any
engineering calculations needed. In fact since weld reinforcement is
not a portion of a perfect circle this approach may be closer to the actual
area/volume!
Having checked several typical weld reinforcements dimensions you
can use 72% of the Area of a Rectangle for the estimate of
reinforcement.
With
these basic shapes you can calculate the area of almost all welds.
Look at
the following examples of the of weld joints; the weld area can be arranged
into Triangles, Rectangles and Segments.
To
calculate the weld metal volume that must be added to a weld joint you simply multiply the
Area times the Length in
the same dimensions. Therefore if the length is given in feet convert it to
inches so all dimensions
are in inches. Therefore Area in2 * Length in = Volume in3.
Remember dimensional analysis
works to check your work in 2 * in = in3.
Calculate Pounds of Welding Materials Needed:
Now the Volume of weld metal you’ll
need to add is known , how much wire will you
need? The following are some material densities:
Steel
weights: 0.284 lb / in3; Aluminum = 0.098 lb / in3
depending
somewhat on alloy and Stainless Steel 0.29 lb / in3 again
depending on the alloy.