|
Submerged Arc Weld “Hard
Spots” Cause Cracking in "Sour Gas" Service |
OVERVIEW:
“Hard
Spots” in submerged arc welds have caused major weld failures. This
problem was identified in the early 1970’s when some weldments failed within
days of being exposed to H2S
(hydrogen sulfide.) This can occur in petrochemical processing and in
pipelines transporting "Sour Gas."
Compared to the much smaller “Hard Spots”
recently reported as problems in welds made in HSLA steel, (Reference 1) the
“Hard Spots” encountered in the submerged arc
welds in question are much harder and much larger!
The above mentioned
article expressed concern that the hard areas in MIG
welds in HSLA steel that caused cracking problems in a H2S
test were about as big as the hardness tester indenter. As can be seen
in micrographs below, “Hard Spots” in a failed sub arc weld
made in large diameter transmission pipe were about 40 times the indenter size!
Those located at the surface are readily seen by eye! |
EARLY 1970’s
Harry Ebert, an Exxon Welding Engineer at
the time, published a paper in 1971 discussing hard welds caused by the use
of “active” bonded fluxes and subsequent rapid weld failures (Reference 2.)
We worked closely with Exxon, the API Vessel Committee and fabricators
defining which combination of fluxes and wires were to be used in the as
welded and stress relived condition for this service.
In 1973 a definitive 22 page technical paper
was published by Kotecki and Howden, working for Battelle Memorial
Institute, regarding submerged arc weld “Hard Spots”
(Reference 3.) It clearly showed failures similar to those discussed by
Ebert and defines the cause as “Hard Spots” in submerged arc welds made with
"active"
bonded fluxes, i.e. those containing Ferro Alloys. A majority of
bonded (also called agglomerated) fluxes contain Ferro Alloys for a
number of flux manufacture and weld performance reasons. The photo
macrograph directly below shows one
figure from the Kotecki/Howden report with cracked “Hard Spots.” They found relatively large, very high Mn and Si “Hard
Spots” in submerged arc welds made with bonded fluxes. These “Hard
Spots.” cracked rapidly when exposed to H2S testing.
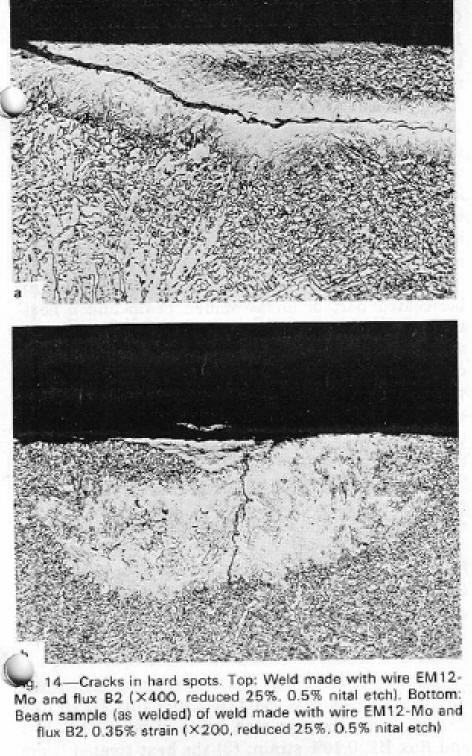
|
1980’s
My early career was in research and
development of the submerged arc welding processes, fluxes and wires. I
presented
technical papers in a number of pipeline conferences on the subject of submerged arc welding
natural gas and oil transmission
pipe with a welding process we developed that welded long seams in UOE pipe at 3000 amps
(Summarized in Reference 4) that doubled
existing welding speeds. At these conferences, several papers addressed steels for use in sour
natural gas
service and the problems with hydrogen sulfide induced cracking. However none discussed possible weld metal problems when subjected
to sour gas.
With my experience with submerged arc weld
“Hard Spots” in pressure vessel failures, I discussed the issue
in visits with all North American pipemills. There were nine UOE
pipe mills in the US and Canada all of whom were using specially designed
high performance fused submerged arc fluxes made especially for this service.
Fused fluxes, as found by Kotecki/Howden did not produce
welds containing “Hard
Spots.”
[ Note: fused fluxes can be fully reacted during manufacture eliminating
the production of metal particles while welding. This compares to
bonded (also called agglomerated) fluxes whose ingredients are first reacted during welding.] At
that time, these UOE pipemills cleaned the steel surface prior to welding. Many used
automatic shot blasting of the complete pipe steel surface which helped with
subsequent corrosion coating as well as weld performance. A
Canadian spiral pipe mill was also manufacturing some natural gas and oil line pipe.
This spiral pipe mill also used fused flux specially designed for gas and
oil pipe production.
Visiting most of the US and Canada UOE natural gas and oil pipemills
several times per year, they were verbally told about the concerns of using
active bonded fluxes for the manufacture of gas and oil pipe that could be used for
transporting sour gas. A spiral pipemill
making some gas and oil transmission pipe decided to use an active bonded
flux apparently to handle the extra mill scale on their plate. They produced pipe for a natural gas
transmission line that was placed
in the Grizzly Valley in Canada. It operated satisfactorily for a period of
time until a gathering line from a gas field containing sour gas was added.
Sections of the
line failed catastrophically within a very short time of being put in sour
gas service. The failure occurred in very long lengths at several
locations!
Little is
written about this major failure for some legal reasons.
However in a
Corrosion Conference held in San Francisco on March 9-13, 1987, a technical
paper was presented and proceedings published (Reference 5.) One of their conclusions
states; "Analysis of failures revealed they (cracks) originated in the inside weld
bead of a spiral weld which contained hard areas of Martensite and/or Banite
with hardness values between 300 and 500 HV." They go on to say pipe
used in this gas line made at another pipe mill (My
Note: no doubt a UOE mill using fused flux, since only this one spiral pipemill was making large diameter gas pipe at that time and all UOE pipemills in North America were utilizing fused flux,)
had no such
“Hard
Spots”
and that pipe, transporting the same sour gas, did not fail.
|
LATE 1999 thru 2000’s
In 1999, with most of the natural gas and oil pipeline
infrastructure in place in the United States, there was only one UOE US pipemill approved for
API gas and oil pipe production (now that pipemill is also closed and dismantled.)
That mill stopped
using their plate surface shot blaster because of high maintenance cost.
Therefore the fused submerged arc flux they had been using was replaced with a bonded flux
to handle the plate mill scale. [Note, bonded
fluxes contain deoxidizers such as Ferromanganese and Ferrosilicon.
These Ferro Alloys combine with iron oxide and prevent CO weld
porosity from forming. However they also produce Mn and Si rich hard
spots!] The flux manufacturer designated this grade as
being designed for pipe manufacture welding. It was an active bonded
flux. We were asked to examine a failed weld made with this flux
causing the pipe to burst open during hydro testing. The pipe had failed
along the full 40 foot weld seam. We observed several large sections with the
crack moving along the weld and in and out of the weld and HAZ. The pipe
mill metallurgist found no issues with the steel different than the
remaining steel used for all of the pipes being produced for the pipe order.
A detailed examination of a small section of
pipe weld we were given showed many “Hard Spots”
on
the surface (about 20 per inch.) An EDAX trace showed them to be very high
in Mn and Si. The hardness of these obviously martensitic areas was 445 VHN.
As seen in the photomicrographs below they were very large, 3 or 4 times
larger than those observed by Kotecki/Howden (Reference 3.)
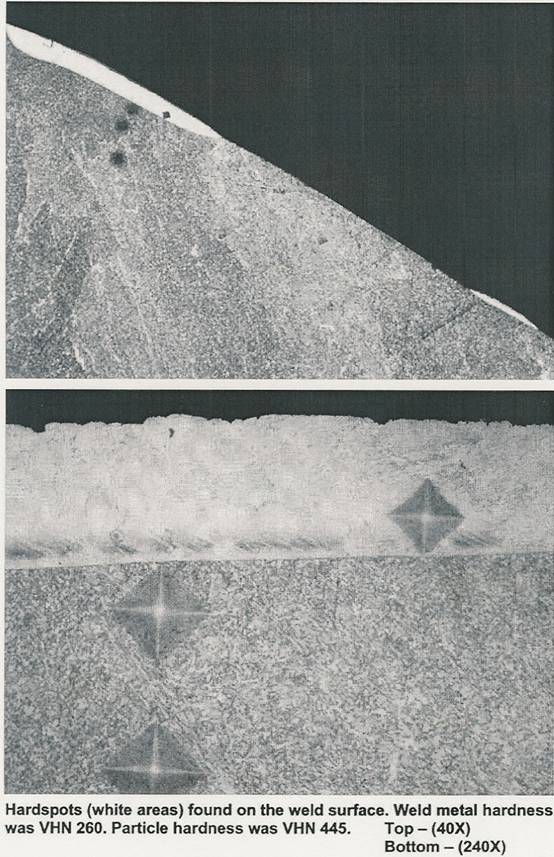 |
HARD SPOT TEST DEFINED
A test for submerged arc weld “Hard
Spots” was developed for a major oil company. They will use
it in specifications for pipe exposed in Sour Gas Service. The test is
simple and involves making a weld pad.
Note About Required
Sour Gas Corrosion Tests: Some of the corrosion test samples
required for pipe used for sour gas service require the weld bead be ground flush
with the plate surface. This can eliminated the offending surface
"Hard Spot!" It is suggested some corrosion tests be made with the
weld reinforcement in place as this is the way the pipe will be used in
service!
|
BOTTOM LINE
Having extensive experience related to the use
of submerged arc welding in the manufacture of natural gas and oil transmission pipe, as well as research experience
and patents for fluxes and wires used for submerged arc welding pipe, I am in a
unique position to define why these “Hard Spots”
exist. I can discuss issues such as flux raw ingredients, raw material sizing, mixing
etc that determine their size and frequency. I can help define
appropriate tests for these “Hard Spots.”
Other welding processes
and consumables could possibly cause similar issues.

Email to discuss
consulting on the subject. |
REFERENCES:
-
“Effect
of Welding Parameters and H2S
Partial Pressure on the Susceptibility of Welded HSLA Steels to Sulfide
Stress Cracking; “by G.M. Omweg, G.S. Frankel, W.A. Bruce, J.E. Ramirez
and G. Koch; AWS Welding Journal, June 2003
-
“Hard Welds -Their Causes and
Prevention,” H. W. Ebert, AWS Welding Journal, September 1971
-
“Submerged
Arc Weld Hardness and Cracking in Wet Sulfide Service,” by D. J.
Kotecki and D. G. Howden, WRC (Welding Research Council) Bulletin Number No.184 (1973)
-
"Three Wire
Submerged Arc Welding of Line Pipe," by G. D. Uttrachi and J. E. Messina,
AWS Welding Journal, June 1968
-
“Pipeline
Failures in the Grizzly Valley Sour Gas Pipeline,” by V. B. Lawson, C.
Duncan, R. S. Treseder; CORROSION/87, paper no. 52, (Houston TX; NACE,
1987)
|
|