Tip of Month Achieve
Don't Use A Flow Rate That Creates Turbulence!
The
typical gas flow rate through a MIG gun is about 30 CFH that is only 0.5 CFM. It is very low, about
a human breathing rate when sitting! There is a maximum flow rate, that if
exceeded, will cause turbulent flow that mixes air into the shielding gas
stream causing weld quality problems. For a typical 5/8 inch ID industrial MIG nozzle size, that
maximum velocity is about 50 to 60 CFH. For a smaller welder using a 1/2 inch ID nozzle the max flow rate is about 40 CFH. Setting flows higher than these rates is counter
productive! (See
reference 4 from The Welding Institute)
Who would use more than these flow levels? The answer is often every MIG welder at the weld start! The reason and way to fix it, is covered in this TIP of the MONTH!
In
addition, some folks when setting shielding gas flow believe, "If some is good, more must be better" - They Are Wrong! |
|
|
Tip of the Month

Calculations of MIG Shielding Gas Use Are Bogus!
They are often low by over 80% !
|
A Patented Gas Delivery
Hose System that:
-
Reduces weld
start
gas surge 80/85%, while providing sufficient extra gas to purge air
from start area.
-
Cuts
total gas use typically in half;
as users who
carefully measured report.
-
Improves
weld start quality, by limiting peak surge flow
rate avoiding turbulence.
-
Maintains preset welding
gas flow rate
by retaining gas pressure to compensate for flow
restrictions.
|
Patented FB3 and FB4 GSS’s are for smaller shops and home welders. "Cuts" gas waste while improving gas "Shield." They assist as skills devlope to make quality, good looking welds or maybe to become a "master welder!"These welders use smaller size gas cylinders and often make shorter welds and tack welds. The “gas blast” at every weld start not only wastes considerable gas, it leads to excess spatter, poor weld shape, and possibly internal porosity. That excess flow rate pulls air into the shielding gas stream. The turbulent flow created lasts for a short time even after flow rate reduces until desired laminar flow is attained. This inferior gas shield exists for much of a short weld! Peak flow rates can exceed 150 CFH.
By saving wasted shielding gas at the weld start, higher gas flows can be used when welding in drafts or outdoors. This provides better weld quality while still using less total gas! |
Testimonials
Al Hackethal sent this email after purchasing a 3 foot, FB3 GSS for his small MIG welder. “Well, I can't believe it. I never thought a hose could make that much of a difference. The weld quality (with the GSS), and even penetration is considerable better. Almost no spatter! Initially thought that my imagination had kicked in, but then realized that the gas I'm buying is actually working the way it's supposed to. Glad I found your website. This is one of the few things that really works better than any info could suggest. I understood the theory, though in practice I understood it much better after the first couple of welds. Now I have better looking welds and almost no spatter, which means less grinding and finish work! In addition, the tip was cleaner after the job I just did.
Another customer, Jason Insley, had this to say “Everything worked fine. And my weld starts have definitely improved since installing the GSS |
In Summary
The GSS cuts gas waste using a small ID, heavy wall thickness hose with a peak flow limiting restrictor. This cuts starting gas surge by 85%.
The GSS provides better quality weld starts by reducing shielding gas turbulence. For short welds excess turbulence can last for much of the weld.
It typically pays for itself in one gas cylinder refill. Over 10,000 are in use.
Instructions supplied with FB3 and FB4 products include shielding tips for smaller welders. Tips like an expalnation of why you should NEVER use a self-shielded flux cored wire in combination with a gas shield! They also provide suggestions when welding outdoors. |
“Cut Gas Waste - Improve Gas Shield”
CLICK to Download PDF of SilverShield GSS Flyer in 2 Column Formate
CLICK to Download PDF of SilverShield GSS Flyer in 1 Column Formate |
|
|
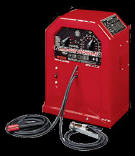
The success of the Lincoln Electric Company is due to the business methods
developed by J. F. Lincoln. He evolved and sustained unique business
practices that allowed Lincoln Electric to be a major factor in the
development of the welding industry. He managed the Company from
1914 until his death in 1965 at age 82. Bill Irrgang succeeded Jim Lincoln
and continued his business philosophies until 1986. The company
adapted to current times and continues to be very successful as a worldwide,
focused welding business.
A summary of the key points of the business management books written by J.
F.
Lincoln and some direct experiences related to the company is available as a
PDF download. The similarities to the management techniques employed
by Henry Ford as well as Fred Taylor's work on scientific management are included.
.
CLICK to Download PDF |
J.
F.
Lincoln�s Management System was threatened by US government policies in the
late 1930�s. He wrote a number of letters and articles about his concerns that
were published in local newspapers. Lincoln Electric workers were doing
well in a period where government intervention was making things worse! One
small section of our review contains quotes of his thoughts. The following
are some quotes abstracted from James Lincoln�s management books and one
written by Virginia Dawson in 1999 entitled �Lincoln-a history.,� All these
books are available from the James F. Lincoln Foundation Library at:
http://www.jflfoundation.com/SearchResults.asp?Cat=24
Many
of his thoughts are applicable to today�s environment!
�For the
first time in American history, free enterprise is being destroyed by
high-minded incompetents who have only the best interest of American at
heart, but whose knowledge of what makes the economy successfully progress
is completely nil.� �Because of this and their soft-hearted �do-gooder�
attitude in which they are perhaps entirely honest, they are destroying
America.�
�Desire for
freedom was why America was founded.� �Our present policy of
government-promised security is providing a race of incompetent softies�
�The program of the various deals, �New� and �Fair� has already stopped and
reversed the development on which we depend for our future progress and
national security.� �We have developed a philosophy which shuns individual
responsibility.� �When all citizens depend on government support, it takes
most of the earnings of most producers to provide a bare living for all.�
�One way to remedy a slip (in
the economy) is to borrow from the future and live at the old rate on
borrowed money.� �The problem with the next generation suffering for our
sins leaves us cold. Why worry about them they are not even born yet.�
�The loafer
should not be allowed to live on the efforts of the worker.� �This is an
easy way out but its national suicide, as history shows.� �Every nation
that has disappeared has gone through the same sequence and the same result;
1st softening of peoples ambition and lessening incentives; 2nd increase
in numbers of people who fail to develop themselves or their latent
abilities; 3rd a feeling of helplessness; 4th public
support for all who ask for it; 5th insolvency of the economy as
fewer will work to care for the careless and because of the softening
process; and 6th being surpassed by a virile nation that has not
gone soft.�
�Few (politicians)
understand what makes free enterprise succeed.� �Will the average person
exercise their responsibility as a citizen of a representative government so
the freedom on which is future depends will continue? Our experience under
Roosevelt and Truman answers the question with a definite NO.� �
Putting the power of the state over the operations of industry is called
socialism by some, communism by others; in actuality, it is called a
totalitarian government where the citizen is a serf of government directed
by bureaucracy.
�No
bureaucrat can operate any industry successfully.� �If the present attitude
in Washington continues this will not be a place where either you or I or
your grandchildren can live with any degree of satisfaction.�
In 1938 Jim
Lincoln retaliated and refused to invest in the USA and visited Australia
where they were rugged individuals. Lincoln worked with a local steel
company who promised to supply the companies product needs. The Lincoln Electric Company (Australia)
Proprietary Limited opened the same year of his visit. Jim Lincoln also
started a business in the England in the 1930�s. However, at the end
of WWII he strongly
disapproved of the elected Labor Government and sold the
business, including the Lincoln name in the UK, for $400,000! |
Totalitarianism-My Experience
My
experience with the effects of totalitarian rule reinforces the illogic of a
central bureaucracy managing the needs and wants of the individual.
In the mid
1970�s we participated in a technical exchange with a famous
Russian welding institute. We both had targeted objectives, ours was
electroslag welding and fused flux manufacture, and theirs bonded flux
manufacture and flux cored wire. After several years, we made little progress. We decided to
keep the last meeting small. Two representatives from Russia came to the
Ohio R&D lab that I managed, a researcher who we had grown to know and the
�interpreter� (who participated in every exchange visit and was actually
more than an interpreter!) We had been told that in a previous visit to our
Ohio Lab they believed we had taken them to the �mayor�s� house for dinner,
as they could not believe it was the home of our business manager. I
decided for this last visit to pick them up at the airport and take them to McDonalds for lunch
to show how the average American ate. During lunch, the researcher asked an interesting
question. What was the difference in pay between our engineers and
technicians? I thought about the salaries, the overtime pay the technician
earned and the increased taxes paid by the engineer because of his salary
level and felt it was about 30%. I then asked what the differences were in
Russia. He said, �Much more and difficult to measure. For example, because
of my position I can get an apartment my technician cannot, he and his
family live with his parents. I can get a new car, it may take 6 months to
a year but I can get on the list, he cannot. Food is inexpensive for both
but for many other products my family gets priority.� I then asked about
the cost of a refrigerator to get a feel for a typical product price. He
said, �Oh refrigerators are very cheap because the central planners made
many more than people need! However, you cannot get a washing machine
because they did not plan enough!� That prompted a conversation in Russian
between him and the �interpreter� which was obviously contentious!
During
that same visit, I had to ask my good friend and Cubin born technician to
stay home because of his expressed passionate dislike of Russians. His
father had a small farm in Cuba and my friend would help pick tobacco from
their field and roll a cigar for his dad. He and some of his family were
able to leave Cuba when the Castro regime took over but his dad stayed. His
farm was taken away from him by the regime but it did not go to the �people�
it went to the communist mayor of the town! My friend�s emotions were so
high, it was better to have him stay home then perform a demonstration for
our guests as had been planned! (Some years later, he was able to get his
dad out of Cuba during the �Freedom Flotilla.�)
A
reinforcement of the effects of central planning occurred in the mid 1980�s
when we had
a welding equipment factory in West Germany. A large welding
fixture builder purchased our US made submerged arc equipment. I was
visiting to discuss a number of multi-electrode welding machines he was
selling to Russia. I asked if it bothered him to sell to the Russians since
it was obvious from his comments he had no love for them! He said, with a
laugh, �No,
because the central planners in Moscow always buy products the fabricating
plant does not need. In addition, by the time they transport the product to
a plant many of the parts are stolen!� (Picture left is the first 3-wire
submerged arc all AC power welding system that welded at 3000 amps making
large diameter natural gas and oil transmission pipe. We developed the
system in the late 1960's and 8 such systems were installed at this US Steel
Pipe Mill in Provo Utah, 11 at Armco Steel in Houston -and in a number of
other pipemills around the world -unfortunately, like
most USA UOE pipemills , those mentioned are no longer in existence!) |
Karl
Marx:
I recall a
biography of Karl Marx I read some years ago. A writer visited his
apartment and said he had to sit in a chair that had dried puss from boils!
Marx and his family lived in squalor! Found the following in the Internet:
�He
was covered with carbuncles, furuncles and boils and he complained about
them in letters. They were painful, and large, and at times a doctor had to
lance and drain them. In describing one such operation, he said the size of
the boil was as big as his wife's fist.
Marx wrote he was covered head to toe in the eruptions. He also wrote
about having them on his backside and his most private parts. Doctors, long
after his death, determined he was suffering from Hidradenitis Suppurativa,
a disease of the sweat glands found in the armpits and groin.� When reading
his writings, I wonder how many folks consider how this may have influenced
or distorted his perspective! |
Some social safety net programs are needed and can be provided by private
charities or the federal government. However an incident reminds me of
the abuses and unintended lifestyle consequences that are created with federal programs
rather than local operated programs or private charities.
I obtained two
masters degrees in the evenings, while working in a welding R&D lab. I
would eat on the run between work and class. The primary "dinner" spot
was a hot dog push-cart operated by an immigrate from a former iron Curtain
country. I recall we would discuss his desire to expand his business
and I suggested buying another cart and hiring an employee. He was
reluctant to trust anyone to be as hard working as he was or to assure
they were honest! He was having to address
some of the risks all entrepreneurs must face!
One evening, a
friend of his was ordering a hot dog and discussing his personal dilemma. He
was complaining that he had two children, a boy and a girl, but his "federal government housing"
only allowed him two bedrooms. The children were getting old enough that
they needed separate bedrooms. The hot dog vendor told his friend, "Well, if you have one more child you'll be eligible for three bedrooms!"
His solution was based on the rules some "bureaucratic do-gooder" thought
were reasonable! But like having more children without being married
allows more government subsidies, this creates inappropriate,
destructive behavior. If the federal government feels obligated to get
involved in these programs, give the monies to state and local governments
where these unintended consequences and irrationalities can be monitored and
funds better
applied. |
Some Thoughts for Today:
It is
currently much easier to start businesses around the world than it was when
Jim
Lincoln
objected to government polices and sought to develop businesses outside the
US. Companies and individuals can leave
an oppressive situation and move offshore.
There
certainly are some inequities in the economy that should be fixed.
Tax loopholes are fostered by
Lobbyists, Lawyers, Accountants and
Politicians who exploit them to
support their jobs! These should be closed. True entrepreneurs
who risk their money should be rewarded with no limit. However
rewarding Wall Street types with huge, unlimited bonuses when they have none
of their own money at risk is irrational. The same applies to
corporate executives when huge unlimited bonuses can be earned with no
personal financial risk. This often promotes very short-term thinking and
possible manipulation of financial results.
For public companies, assuring
the appropriateness of top executive salaries
is the role of the Board of Directors employing compensation committees
and proper salary surveys. Stockholders should insist these tasks be
appropriately structured, which is current law. For a vast majority of companies,
executive salaries and bonuses
are appropriate and are
being properly scrutinized. The
Board of Directors must be held accountable for abuses. However making
more complex laws in attempt to "manage" this function just leads to unintended
consequences. Just like NASCAR racing, make the rules apparently very
restrictive and racers still find ways to get around them-legally! It�s a
game! That is what is happening in Washington DC;
Lobbyists, Lawyers, Accountants and
Politicians become rich finding ways around complex unneeded laws!
Revise the tax code, be it a
multilevel flat tax or whatever-but make it simple.
Fabricators: The following is a way to save
shielding gas waste and significant cost so you can be more competitive and
hire more folks! |
|
|
|
High Waste Case:
To evaluate a high waste case, assume gas waste is the high side
defined in the literature, i.e. gas usage is 6 times what is needed with a
high duty cycle which reduces Labor Percentage.
Shielding gas would now be
32% of welding costs!
Probably higher than actual
unless your welders are also setting much to high a flow rate.
See Details of Calculations
Used for This Information: |
NO
Gas Waste Case:
Most MIG gas use calculations make no consideration for
shielding gas waste. The resulting weld cost pie chart
is shown on the left. This is what is typically published as a way
of calculating shielding gas costs.
Shielding gas is
shown as only 5 % of total cost and less than wire costs which are 7%.
This is based on an unrealistic assumption of no
gas waste.
It�s Bogus! |
Don�t feel badly if you
find out your using far more gas than you should! An analysis done
for a major fabricator showed they were wasting 83% of their Argon and 90%
of their CO2! In addition to the high gas surge at
the weld start they were setting excess flow rates and they also had leaks.
Want information on how to
measure and monitor leaks on an ongoing bases?
CLICK TO SEE our Lean Welding
Manufacturing Self Study Programs related to gas us age.
Click
on Email ICON and ask for more information.
-
Weber, R., How
to Save 20% on Welding Costs. Trailer/Body Builders, Volume 44, Number 3,
January 2003
-
Standifer, L.
R., Shielding Gas Consumption Efficiency. The Fabricator, Volume 30,
Number 6, June 2000.
|
MIG Shielding Gas Flow Control is Much
More Complex Then it Appears |
The first Gas Saver System Video shows our ’34 Pro Street Rod with its sound system playing "Roll Over Beethoven." That song referred to Beethoven rolling
over in his grave if he heard Rock and Roll! A comment followed saying the famous fluid mechanics scientist who defined the basic equations that make airplanes fly in the 1700's, Daniel Bernoulli, would "Roll Over in His Grave" because of our
lack of understand of MIG shielding gas control and the cause of very
high gas waste!
MIG gas flow control is much more
complex than it first appears. We’ll provide a quick overview and link to
other pages in this website for more details if you want to understand it
fully.
|
The
gas flow rate through a MIG gun at 30 CFH is only 0.5 CFM. It is very low, about
a human breathing rate when sitting! There is a maximum flow rate, that if
exceeded, will cause turbulent flow, which mixes air into the shielding gas
stream causing weld quality problems. For a typical 5/8 inch ID industrial MIG nozzle size, that
velocity is about 50 to 60 CFH. Setting flows higher than that level is counter
productive! (See
reference 4 from The Welding Institute)
Who would use more than these flow levels? The answer is, often every MIG welder at the weld start! The reason is covered below! In
addition, some folks believe, "if some is good, more must be better" when it
comes to shielding gas flow-they are wrong! |
An important factor is the
pressure needed in the gas delivery hose to flow gas through a welding machine
(or wire feeder,) MIG gun
cable, gun and nozzle will vary from about 3 to 7 psi. The
amount needed will change as
flow restrictions change when welding. These flow restriction changes are caused
by:
a) bends of the small gas passage in the gun
cable,
b) spatter blocking one or more of the small gas diffuser holes, 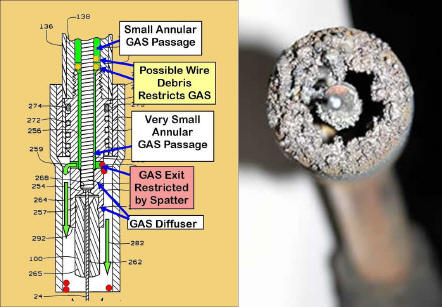
c) spatter build-up in the nozzle, and
d) since, in most MIG gun cables, the gas hose doubles as the holder of the spiral wire liner; wire drawing compound, shop dust and copper flakes
from a steel wire that build up in that
area.
They not only cause wire feeding problems they cause flow restrictions! |
With
these flow restriction changes the flow rate set with a flowmeter needle valve or
an orifice in a regulator/flowgauge would cause
the flow to vary significantly. The engineers who designed the MIG flow control
system when the process was introduced, knew this was a problem and employed a
flow control approach that would automatically compensate for restrictions downstream of
the flow control device. The approach used relies on the fact
that the speed of the a gas through a small opening in a needle valve or
orifice cannot exceed the speed of sound! When the speed of sound is
reached, that speed in a
small opening is what controls flow and it does not depend on the downstream
pressure. To achieve what is called "choked flow" that provides
this Automatic Flow Compensation, the absolute pressure (gauge pressure + atmospheric pressure) upstream
of the flow control device must be 2.1 times the absolute downstream
pressure. Using 2:1 for an approximate calculation, see figure below
for the pressure required: |
The figure left shows the pressure needed to achieve
"choked flow" is 25 psi. It is no coincidence that quality flow
controls shown in this picture use pressures from 25 to 80 psi.
The engineers that designed MIG and TIG flow control systems when these processes were introduced, knew of the varying flow restrictions and designed to automatically compensate so flows remained at the initial settings.
|
If high pressure solves the consistent flow problem, is there
a downside? Yes, when welding stops and the solenoid closes in the
welder or wire feeder, gas continues to flow though the needle valve or
orifice and quickly fills the gas delivery hose with more gas which raises the pressure.
It reaches the pressure of the regulator or pipeline. This
stores a lot of excess gas equal to, in the case right (80+15)/(4+15) = 5
times the hose volume of excess gas. We also find a typical 1/4 inch ID
hose expands another 13% at the high pressure. Therefore, the excess gas in the
hose is 5 x 1.13 = 5.7 the physical hose volume!
However using pressure less than 25 psi, as some have tried with devices
like "Gas Guards" creates bigger, less obvious problems than what they are trying
to solve! This eliminates Automatic Flow Compensation causing wide variations in flow. See test result comparisons of a proper flow control
with a commercial low pressure device.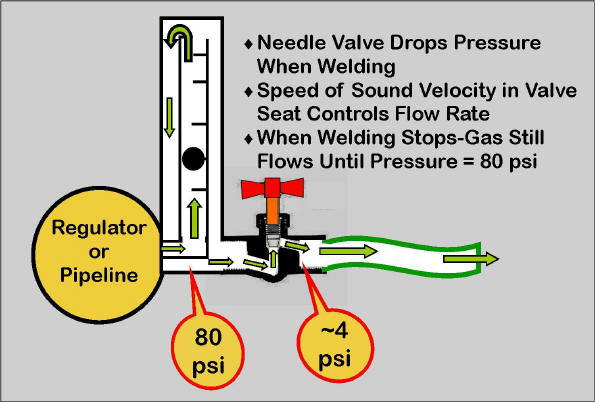 |
That excess gas, stored in the gas delivery hose when welding stops, "blasts out"
of the MIG nozzle at each weld start! This high flow not only wastes gas but the
high velocity (we have measured peak flows exceeding 200 CFH) creates a high
degree of turbulence that causes air to
be pulled into the shielding gas stream. The air causes problems with
weld quality and produces excess spatter. This gas waste can be over
half the total gas used.
The solution to the gas waste and high peak gas surge
is our patented Gas Saver System.
It is a simple, custom extruded, small ID, heavy wall gas delivery hose with
a peak flow limiting orifice built into in the welder/feeder end brass
fitting. It maintains system pressure and therefore Automatic Flow Compensation.
The controlled small amount of extra gas it retains, quickly purges air from the
weld start zone and MIG gun nozzle. Purging air
from the weld start area and gun nozzle is essential for quality weld
starts.
Some devices have been tried over the years that attempt to control flow at the wire feeder or welder to eliminate surge and have been rejected by welders! We used to agree with management believing welders just didn't care about "saving gas." Since forming WA Technology and working with a number of welders in production operations related to gas flow control we have found they were right! These devices such as Simple Orifices, Flowmeters or Regulators with Orifice Control that are mount at the wire feeder do not provide the needed extra start gas. Stauffer in a 1982 patented device discussed the issue and added a reservoir to hold and deliver some extra start gas! When encountering flow control at the wire feeder welders either drill out the orifice or if a flowmeter or regulator mounted at the wire feeder is being used they increase the steady state flow in attempt to compensate! They may not even know they are trying to provide some extra purge gas but they see the inferior weld start result and attempt to compensate for the lack of purge gas! Increasing the steady state flow DOES NOT fully solve the lack of some extra start gas and it WASTES RATHER THAN SAVES GAS! IT DEFEATS WHAT THE MANAGEMENT WAS ATTEMPTING IN THE FIRST PLACE!
CLICK TO SEE DOCUMENTED CASES OF THE PROBLEMS WITH LACK OF START GAS
CLICK TO SEE WHY WE SELL DIRECTLY ON THE INTERNET AND NOT IN "STORES'"
The patented Gas Saver System :
1) Quickly supplies a controlled amount of extra start gas purge at each weld start and
2) Controls the maximum gas velocity of the extra start gas with a
peak flow control orifice that avoids excess turbulence. Improved weld starts result.
Note, the peak flow control orifice does not control the steady state flow while welding - that is set by the
existing conventional gas flow control device. For cylinder gas supply
that can be a regulator/flowmeter or a regulator/flowgauge. On pipeline
supply it can be a flowmeter or simple orifice located at the pipeline drop. It will prevent setting very high excessive flow rates if that is an issue. |
You can Google these names to see their contribution to the understanding
of gas flow. They may not have used the words "choked flow" but all
would understand what it accomplished and why it would be needed in MIG
welding flow controls!
Galileo
Galile
1563-1642
Was one of the
early contributors to understanding sound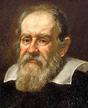
Daniel
Bernoulli
1700-1782
Pioneer in fluid
mechanics. We use his work to define how airplanes fly!
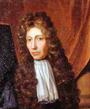
Robert Boyle
1627-1691

Herman Helmholtz
1821-1894
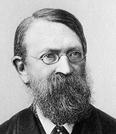
Ernest Mach
1838-1916
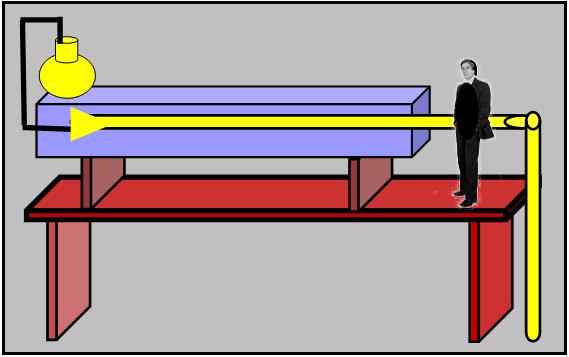
Osborne Reynolds
1842-1912
|
|
Don't
Tolerate Gas Leaks!
Leaks work 24/7 and also allow
moisture laden air to enter the gas pipeline. |
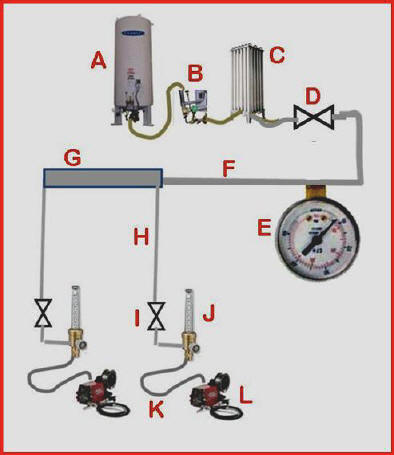
Schematic- Pipeline
Gas
Supply
A= Liquid Tank
B= Economizer
C= Evaporator
D= Shut-off Valve
E= Pressure Gauge
F= Pipeline
G= Header
H= Pipeline Drops
I= OSHA Required Valves
J= Flowmeter
K=Gas Delivery Hose
(Preferable our Gas Saver System)
L= MIG Feeder
|
Evaluating fabricators
gas usage, some are wasting considerably more shielding gas than the
apparently accepted 3 to 5 times what they could use! Many accept that
they have pipeline and hose leaks. However few have quantified how
much gas these leaks are causing! |
Pipeline Leaks:
We
have defined a simple method of quantifying the amount of gas leaking from
pipelines, gas delivery hoses, fittings and MIG feeders.
It is a Leak Down test used very effectively in regulator manufacture.
The method can be quickly used as an ongoing check for leaks. |
Our
"Lean Welding
Manufacturing-Shielding Gas" Learning Program defines this Leak Measurement
approach as well as many other gas cost related issues. It is a 70 +
page document and includes an Excel Spreadsheet that helps make measuring
gas leaks relatively easy. |
It also provides the following:
 |
Information on weld
problems associated with excess gas use. |
 |
Method
to check gas flow rates at the MIG gun nozzle and compare flows entering
the MIG feeder. |
 |
Suggested
approach to plot purchase data of wire and gas each month to keep a focus on
gas waste problems and monitor results for each welding machine. |
 |
Example tables show ways of developing moving average purchase data of wire and gas
that can
be recorded and maintained. |
 |
Ways to find leaks including using an Ultrasonic leak detector. |
 |
Examples of fabricators gas usage and savings are detailed. |
 |
Information showing why a 0.035 inch diameter leak in a 50 psi gas pipeline or hose
can cost over $14,000/year. |
 |
5 pages of
Questions
and answers on separate sheets to evaluate comprehension of
the information provided. |
CLICK TO SEE PROGRAM DETAILS AND HOW TO PURCHASE |
Cryogenic Tanks: We receive a number of
inquiries
about liquid gas tank
losses and questions such as; "Should pipelines be shut-off from the
liquid supply over a weekend?" Discussions with an engineer
from the leading US cryogenic tank producer provided some interesting
information. However since most of these tanks are rented to a
fabricator by the gas seller, the following is mostly useful in discussions with your supplier about the situation.
Liquid Argon
is stored at about -300 deg F. The storage tanks use several methods to
insulate the very cold liquid. They have an evaporation rate from
about 1/2 %/day of their full rated volume (for modern new
tanks) to 2 %/day or more for older tanks. Therefore a 3,000 gallon tank (325,000 CF @
atmospheric pressure and temperature, STP) when not flowing gas will
evaporate 6500 CF/day with a 2% evaporation rate and only 1600 CF/day with a
1/2 % evaporation rate.
Some newer higher
efficiency tanks also incorporate
an "Economizer Circuit" (Photo Right) This is how it works: Cryogenic
tanks operate at
125 psi. They vent gas when the pressure exceeds 250 psi. The
pressure increases as heat inevitably enters the tank and evaporates some
liquid. The "Economizer
Circuit" delivers the higher pressure gas to the pipeline (F in Schematic
at top of page)
before sending liquid to the Evaporator (D in above schematic.) The
system utilizes this gas rather than vent it to the atmosphere. These
tanks can also retain Argon for a weekend without or with minimum venting to the
atmosphere!
This assumes the tank is properly sized (not excessively large) and is, on
average, half full.
Bottom Line: Disconnecting
a pipeline from the gas supply over a weekend requires significant purging
on start-up
to remove the moisture laden air that flowed back through the leaks.
The use of a modern cryogenic tank and fixing leaks is the proper solution! |
|
|
Calculations
of MIG Shielding Gas Use Are Bogus!
They are often low by over 80% !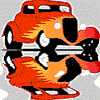
Test
|
First,
evaluating the simplistic approach typically published:
General
Assumptions:
-
0.035 diameter solid wire
operating at 190 amps. That deposits 5.5 lbs/hr when the arc is on.
Assume wire cost is $0.85/pound
-
30 CFH Shielding Gas flow setting.
Assume a cost of $0.10/cubic foot for an argon based gas (= $10.00/100
cubic feet)
-
Direct Labor cost = $18.00/ hour
-
Labor Overhead = 30% of Labor cost
|
NO
Gas Waste Case:
With the above assumptions and no consideration for
shielding gas waste, the resulting weld cost pie chart
is shown on the left. This is what is typically published as the
method of calculating shielding gas costs.
It�s Bogus! |
Shielding gas is
shown as only 5 % of total cost and less than wire costs which are 7%.
This is based on an unrealistic assumption of no
gas waste.
|
High Waste Case:
To evaluate a high waste case, assume gas waste is the high side
defined in the literature, i.e. gas usage is 6 times what is needed with
a high duty cycle which reduces Labor Percentage |
Shielding gas would now be
32% of welding costs!
Probably higher than actual
unless your welders are also setting much to high a flow rate.
|
Where Does the Extra Gas Come
From and Go?
Each time welding stops a
significant amount of excess gas fills the delivery hose from gas source to
feeder. This excess is expelled at high velocity at every weld start.
An example of a fabricator who tested our Gas Saver System (GSSTM)
provides a graphic picture of how much gas is wasted at the weld start.
This
manufacturer of truck boxes selected a repetitive job of welding doors.
They put a full cylinder of shielding gas on one welding system with
the existing gas delivery hose. They welded 236
doors with that cylinder. They then put on a new full
cylinder and our
GSS
with no changes in gas flow setting or welding procedures. When the cylinder was
empty they had welded 632 doors!
That is 2.7 times more parts or said another way they were wasting 63% of
the gas they were using!
Note: gas leaks, high gas flow settings etc, are not part of this test.
The savings they achieved were just from reduced gas surge at the weld start!
CLICK
to SEE many more production examples at:
|
Another reason for gas
waste is welders often believe �If some is good more must be better,�
when it comes to setting gas flow rates. With typical flowmeters we have
measured 150 CFH flow at the MIG Gun nozzle when the needle valve was fully opened. The article
mentioned above
(Reference 2
) stated in hundreds of surveys he performed only 20% had settings that
were at the correct level! We have observed many MIG machines with the float ball
pinned to the top of the tube! We have a recently patented locking system that
fits most flowmeters and blocks flow increases beyond what is desired.
CLICK to SEE this product. |
Want to
calculate your gas usage and define how much is waste?
CLICK to GO TO
this
web page and download the FREE �Guide to Saving Gas.� |
Don�t feel badly if you
find out your using far more gas than you should! An analysis done
for a major fabricator showed they were wasting 83% of their Argon and 90%
of their CO2! In addition to the high gas surge at
the weld start they were setting excess flow rates and they also had leaks.
Want information on how to
measure and monitor leaks on an ongoing bases?
CLICK TO SEE our Lean Welding
Manufacturing Self Study Programs related to gas us age.
Click
on Email ICON and ask for more information.
-
Weber, R., How
to Save 20% on Welding Costs. Trailer/Body Builders, Volume 44, Number 3,
January 2003
-
Standifer, L.
R., Shielding Gas Consumption Efficiency. The Fabricator, Volume 30,
Number 6, June 2000.
|
Tip of the Month
Why Welders "Love" Our
GSS
(And "Reject" Other Attempts to Control
Gas Surge!) |
Have Your Welders Rejected Previous Attempts at Using a Device that was
Supposed to Save Shielding Gas?
"They Were Probably Right!" |
Did
you try an Orifice mounted at the wire feeder to set gas flow rate?
This approach doesn't supply sufficient extra
gas at the weld start to purge air from the torch nozzle and weld start area.
This causes excess spatter and poor starts.
Welders often drill them out in attempt to compensate. That doesn't
fully solve the lack of start gas problem and worse causes higher gas flow
than needed when welding - wasting more gas!
See Why Some
Use of an Orifice Gives False Impression of Saving Gas! |
Have
you tried a "Low Pressure" Regulator/Flowmeter or Regulator/Flowgauge?
Some manufacturers label them "Non
Compensated" which means you don't have the "Automatic Flow Compensation"
built into MIG flow control systems since the process was invented in the
1950's! Click to see what
Automatic Flow Compensation is all about. Understand
why you need it to keep your flow rate constant when spatter builds in the
torch nozzle or when the torch cable with its small gas passage is twisted and
bent as welders perform their normal work.
Welders may try to compensate for the inevitable flow changes by
setting the steady state flow higher wasting gas! |
Did
you try a surge flow reducing device with Both Problems - a Low Pressure
Device Mounted
at the Feeder?
It not only doesn't deliver enough extra start gas, the low pressure
eliminates "Automatic Flow Compensation."
See test results with this
product that produced flow varying from 16 CFH to 37 CFH when subjected to a
range of flow restrictions that might be encountered in production. While the flow
variations were occurring, the flow calibrated pressure gauge read a steady
31 CFH! You would not know the flow variations were happening except
for the inferior weld results! Welders may set high flow rates to
compensate for the low flow encountered when restrictions are present.
Be Careful - Some
manufactures do not mention that the device uses low pressure to control flow.
See production problems reported with this system causing them to be discarded. |
Our
Patented Gas Saver System (GSS
) has
neither problem encountered with the above devices - or any other problems! (Picture shows Sue
holding 25 GSS's ready to be
installed at a welding school.)
First, it provides a controlled amount of
extra gas at the weld start to quickly purge the torch nozzle and weld start
area. The extra gas flow rate is controlled to avoid excess turbulence
with a surge flow limiting orifice.
Second, It does not alter the system
pressure so "Automatic Flow Compensation" is maintained as was
incorporated in quality flow control systems since MIG was invented in the
1950's! This retains the preset flow when spatter builds
in the torch nozzle and diffuser or as the small gas passage in the torch
cable is bent and twisted as the welder moves. Whatever flow the
welder sets is automatically maintained.
It does all this
while reducing the amount a excess stored gas by over 80% compared to
conventional gas delivery systems. It is simple to install by replacing
the existing gas delivery hose. This is accomplished with no moving
parts to wear or knobs for welders to adjust. It improves weld start
quality and does not interfere with the welders ability to set the gas flow
desired.
Thousands are in use
in industrial fabrication shops with gas savings of 40 to 50% typically
reported. One customer provided their test data showing a 63% gas savings.
See 14 documented gas saving
testimonials including detailed test data.
WELDERS LOVE THE RESULTS!
SEE AN OVERVIEW OF HOW THE GSS WORKS. |
First,
evaluating the simplistic approach typically published:
General
Assumptions:
-
0.035 diameter solid wire
operating at 190 amps. That deposits 5.5 lbs/hr when the arc is on.
Assume wire cost is $0.85/pound
-
30 CFH Shielding Gas flow setting.
Assume a cost of $0.10/cubic foot for an argon based gas (= $10.00/100 cubic
feet)
-
Direct Labor cost = $18.00/ hour
-
Labor Overhead = 30% of Labor cost
|
|
Did
you try an Orifice mounted at the wire feeder to set gas flow rate?
This approach doesn't supply sufficient extra
gas at the weld start to purge air from the torch nozzle and weld start area.
This causes excess spatter and poor starts.
Welders often drill them out in attempt to compensate. That doesn't
fully solve the lack of start gas problem and worse causes higher gas flow
than needed when welding - wasting more gas!
See Why Some
Use of an Orifice Gives False Impression of Saving Gas! |
Have
you tried a "Low Pressure" Regulator/Flowmeter or Regulator/Flowgauge?
Some manufacturers label them "Non
Compensated" which means you don't have the "Automatic Flow Compensation"
built into MIG flow control systems since the process was invented in the
1950's! Click to see what
Automatic Flow Compensation is all about. Understand
why you need it to keep your flow rate constant when spatter builds in the
torch nozzle or when the torch cable with its small gas passage is twisted and
bent as welders perform their normal work.
Welders may try to compensate for the inevitable flow changes by
setting the steady state flow higher wasting gas! |
Tip of the Month
Why Welders "Love" Our
GSS
(And "Reject" Other Attempts to Control
Gas Surge!) |
Have Your Welders Rejected Previous Attempts at Using a Device that was
Supposed to Save Shielding Gas?
"They Were Probably Right!" |
Did
you try an Orifice mounted at the wire feeder to set gas flow rate?
This approach doesn't supply sufficient extra
gas at the weld start to purge air from the torch nozzle and weld start area.
This causes excess spatter and poor starts.
Welders often drill them out in attempt to compensate. That doesn't
fully solve the lack of start gas problem and worse causes higher gas flow
than needed when welding - wasting more gas!
See Why Some
Use of an Orifice Gives False Impression of Saving Gas! |
Have
you tried a "Low Pressure" Regulator/Flowmeter or Regulator/Flowgauge?
Some manufacturers label them "Non
Compensated" which means you don't have the "Automatic Flow Compensation"
built into MIG flow control systems since the process was invented in the
1950's! Click to see what
Automatic Flow Compensation is all about. Understand
why you need it to keep your flow rate constant when spatter builds in the
torch nozzle or when the torch cable with its small gas passage is twisted and
bent as welders perform their normal work.
Welders may try to compensate for the inevitable flow changes by
setting the steady state flow higher wasting gas! |
Did
you try a surge flow reducing device with Both Problems - a Low Pressure
Device Mounted
at the Feeder?
It not only doesn't deliver enough extra start gas, the low pressure
eliminates "Automatic Flow Compensation."
See test results with this
product that produced flow varying from 16 CFH to 37 CFH when subjected to a
range of flow restrictions that might be encountered in production. While the flow
variations were occurring, the flow calibrated pressure gauge read a steady
31 CFH! You would not know the flow variations were happening except
for the inferior weld results! Welders may set high flow rates to
compensate for the low flow encountered when restrictions are present.
Be Careful - Some
manufactures do not mention that the device uses low pressure to control flow.
See production problems reported with this system causing them to be discarded. |
Our
Patented Gas Saver System (GSS
) has
neither problem encountered with the above devices - or any other problems! (Picture shows Sue
holding 25 GSS's ready to be
installed at a welding school.)
First, it provides a controlled amount of
extra gas at the weld start to quickly purge the torch nozzle and weld start
area. The extra gas flow rate is controlled to avoid excess turbulence
with a surge flow limiting orifice.
Second, It does not alter the system
pressure so "Automatic Flow Compensation" is maintained as was
incorporated in quality flow control systems since MIG was invented in the
1950's! This retains the preset flow when spatter builds
in the torch nozzle and diffuser or as the small gas passage in the torch
cable is bent and twisted as the welder moves. Whatever flow the
welder sets is automatically maintained.
It does all this
while reducing the amount a excess stored gas by over 80% compared to
conventional gas delivery systems. It is simple to install by replacing
the existing gas delivery hose. This is accomplished with no moving
parts to wear or knobs for welders to adjust. It improves weld start
quality and does not interfere with the welders ability to set the gas flow
desired.
Thousands are in use
in industrial fabrication shops with gas savings of 40 to 50% typically
reported. One customer provided their test data showing a 63% gas savings.
See 14 documented gas saving
testimonials including detailed test data.
WELDERS LOVE THE RESULTS!
SEE AN OVERVIEW OF HOW THE GSS WORKS. |
First,
evaluating the simplistic approach typically published:
General
Assumptions:
-
0.035 diameter solid wire
operating at 190 amps. That deposits 5.5 lbs/hr when the arc is on.
Assume wire cost is $0.85/pound
-
30 CFH Shielding Gas flow setting.
Assume a cost of $0.10/cubic foot for an argon based gas (= $10.00/100 cubic
feet)
-
Direct Labor cost = $18.00/ hour
-
Labor Overhead = 30% of Labor cost
|
Did
you try a surge flow reducing device with Both Problems - a Low Pressure
Device Mounted
at the Feeder?
It not only doesn't deliver enough extra start gas, the low pressure
eliminates "Automatic Flow Compensation."
See test results with this
product that produced flow varying from 16 CFH to 37 CFH when subjected to a
range of flow restrictions that might be encountered in production. While the flow
variations were occurring, the flow calibrated pressure gauge read a steady
31 CFH! You would not know the flow variations were happening except
for the inferior weld results! Welders may set high flow rates to
compensate for the low flow encountered when restrictions are present.
Be Careful - Some
manufactures do not mention that the device uses low pressure to control flow.
See production problems reported with this system causing them to be discarded. |
Our
Patented Gas Saver System (GSS
) has
neither problem encountered with the above devices - or any other problems! (Picture shows Sue
holding 25 GSS's ready to be
installed at a welding school.)
First, it provides a controlled amount of
extra gas at the weld start to quickly purge the torch nozzle and weld start
area. The extra gas flow rate is controlled to avoid excess turbulence
with a surge flow limiting orifice.
Second, It does not alter the system
pressure so "Automatic Flow Compensation" is maintained as was
incorporated in quality flow control systems since MIG was invented in the
1950's! This retains the preset flow when spatter builds
in the torch nozzle and diffuser or as the small gas passage in the torch
cable is bent and twisted as the welder moves. Whatever flow the
welder sets is automatically maintained.
It does all this
while reducing the amount a excess stored gas by over 80% compared to
conventional gas delivery systems. It is simple to install by replacing
the existing gas delivery hose. This is accomplished with no moving
parts to wear or knobs for welders to adjust. It improves weld start
quality and does not interfere with the welders ability to set the gas flow
desired.
Thousands are in use
in industrial fabrication shops with gas savings of 40 to 50% typically
reported. One customer provided their test data showing a 63% gas savings.
See 14 documented gas saving
testimonials including detailed test data.
WELDERS LOVE THE RESULTS!
SEE AN OVERVIEW OF HOW THE GSS WORKS. |
Calculations
of MIG Shielding Gas Use Are Bogus!
They are often low by over 80% !
|
Typical
welding cost calculations show MIG shielding gas is 4 to 5% of the total
welding cost. That�s an approach employed if your selling gas!
The method often
used to �estimate� shielding gas usage is to state, as an example: "If the flow rate is 35
CFH and the duty cycle is 30% (30% of the day the arc is actually on, versus
fitting a joint, moving to the weld location, chipping etc.) That means
each welder is using 35 CFH x 8 hr work day x 30% arc on time or 84 cubic
feet of gas used per day. Sound right? It's way off!
|
Gas Use is in Reality - Far More! Why??
Reviewing
what two published reports say about the amount of MIG
shielding gas used by the average fabricator.
An article in
Trailer Body Builders magazine quotes a representative from
Praxair indicating their market survey findings show the average
fabricator using MIG welding consumes 6 times the
amount of shielding gas theoretically needed. (Reference 1)
Another article
in The Fabricator magazine confirmed this finding of up to 6
times the needed shielding gas being used in fabrication shops.
This
article discuses and quantifies a major reason for gas waste being the high
gas flow surge at the weld start. He also states companies can cut their gas
use in half. (Reference 2) |
|
Useable Flow
Rates
|
Minimum and
Maximum Suggested Flow Rate Ranges
A number of variables effect the
minimum and maximum usable flow rate. These include:
 |
welding current |
 |
torch nozzle size |
 |
joint type (fillet welds require less than
butt welds) |
 |
environment (drafts etc) |
Considering typical environments the
following are suggested:
-
For a 1/2 Inch ID Nozzle;
 |
Minimum Flow Range =
20 to 25 CFH |
 |
Maximum Flow Range =
40 to 45 CFH |
For a 5/8 Inch ID Nozzle;
 |
Minimum Flow Range =
25 to 30 CFH |
 |
Maximum Flow Range =
50 to 60 CFH |
For a 3/4 Inch ID Nozzle;
 |
Minimum Flow Range =
35 to 40 CFH |
 |
Maximum Flow Range =
60 to 70 CFH |
|
High Surge Flow
at Weld Start
Reviewing the above data it
becomes obvious that the high flow surge at the weld
start causes air to be pulled into the shielding gas stream and creates
inferior weld starts. Osborn Reynolds
found in his early work that once started, Turbulent flow takes a short time
to return to Laminar flow after the flow rate is returned to a Laminar flow
level.
One visible
result of the highly turbulent shielding gas flow at the weld start is excess weld spatter.
In a number of applications we have measured 200 to 250 CFH surge flow at
the weld start (systems with longer hoses and/or higher pressures.) This not only wastes gas but also causes inferior weld
starts and internal if not external weld porosity. The accompanying
graph shows the start surge flow with a standard 25 foot, 1/4 inch ID gas
delivery hose and a 5/8 inch ID torch nozzle. Note, the blue line
shows flow with a standard gas delivery hose with the peak flow at 140 CFH. It exceeds the 60 CFH maximum suggested flow
rate for about 2 seconds. The graph in green was made with the same flow
settings and same length Gas Saver System. Note the peak
flow is about 60 CFH and quickly falls below 50 CFH. In addition to
saving about 80% of the gas waste each time the torch switch is pulled, it still provides some extra gas at the
weld start to purge the weld start area, etc. (SEE
WHY EXTRA GAS AT THE WELD START IS IMPORTANT.) In addition
the Gas Saver System does not alter the delivery hose pressure so Automatic
Flow Compensation is maintained; a feature built into MIG gas delivery systems since the
introduction of that welding process.
(CLICK TO SEE WHAT
AUTOMATIC FLOW COMPENSATION IS ABOUT ) One fabricator performing weld repairs found
significant reduction in their weld start rejects when our Gas Saver System
was used. CHECK OUT
THE SPECIFICS. |
MIG shielding gas surge at the weld start is recognized as causing problems. Attempts have been
made over the years to control the high flow start surge to reduce:
1. Turbulence
that causes moisture laden air to be drawn into the shielding
gas stream
creating excess starting spatter and internal weld porosity.
2. Gas
waste that accompanies the start gas surge (we have found this can be 50+%
of overall gas usage!) |
The
patented Gas Saver System (GSS
) is the first device to solve problems associated with gas surge without
causing further problems! It increases weld start quality while providing a total shielding
gas savings up to 50+%!
Example of
a welder that "Loves" our GSS
Welders love the system since it:
1. Does
not limit their options or interfere with their ability to adjust the steady
state gas flow (If you want to limit flow adjustment see our patent pending
Flow Rate Limiter.)
2. Improves
weld starts by limiting peak surge flow rate to a level that does not create
excess turbulence in the shielding gas stream. Sufficient extra gas is
delivered
at the weld start
to purge the torch nozzle and start area of moisture laden air.
3. Maintains
preset gas flow rate even when spatter builds in the torch nozzle or the
torch gas hose becomes bent and twisted in the normal course of doing their
job (this is what is referred to as
�Automatic Flow Compensation" even though most welders and even
some welding
engineers never heard of the term!)
4. Is
of rugged construction with a very heavy wall thickness, fiber
reinforcement hose allowing it to be dragged on the shop flow without excess
wear. It can be stepped on without restricting gas flow!
5. Has
no knobs to
adjust or moving parts
to wear or require maintenance.
|
However
other attempts to solve start gas surge problems are frequently rejected
since they produce unacceptable results. Not understanding the
relatively complex cause
of these issues has frustrated welding foreman and welding engineers to
blame welder attitude - when the welder was actually right!
A
review of some of the problems created by past attempts at solving weld
start surge flow and gas waste follows: |
Use of Fixed Orifice to Limit Surge Flow
A
simple surge flow restriction orifice can be added to the wire feeder to
limit high gas surge at the weld start (we have measured
surge peaks over 250 CFH in some applications which is much higher than the
level needed to avoid excess turbulence!) On the surface sounds like a
reasonable way to limit peak flow, but it creates other problems! The
restrictor can be implemented in two ways:
- The
surge limiting orifice can be sized to limit peak flow while still
controlling the steady state flow at the gas cylinder with a
regulator/flowmeter of regulator flowgauge or at
a pipeline gas drop using a flowmeter.
a. Properly
sized this can work to reduce the undesirable effects of gas surge and
improve weld start quality. However even if sized correctly
when welding stops gas still builds
in the delivery hose from gas supply to feeder. It is still wasted when
welding starts! However rather than in a very short time with the very
high
gas surge it flows at the higher than steady state setting until the excess
gas is gone.
The waste still occurs it just takes somewhat longer and is
less obvious!
b. However
we often find the orifice size is selected so the peak surge flow is set too
low to fully purge the weld start area of moisture laden air. The high flow
surge that caused start problems is eliminated but moisture laden air is
still in the start area and causes similar weld start quality problems! Stauffer in his 1982 patent clearly defined this need, See what Stauffer
said.
Welders often can see this problem and counter by drilling out the orifice
to �get more gas.� What they are doing is counterproductive but they
are seeing the poor initial gas shielding and trying to solve the problem.
See a production
example of a similar problem solved with our GSS.
-
Another way an orifice is implemented is to select a size
that not only controls peak start surge flow but also sets the
steady state flow rate. Now there is not enough extra gas at the weld
start which creates a greater problem (defined in 1 (b) above.)
See a production example of
this problem solved with our GSS.
In addition to insufficient gas at the weld start to purge
the weld start area, torch nozzle, etc (often causing welders to drill out
the added orifice); if on a pipeline gas supply as the pressure reduces
when additional welders are in use
the flow rate changes.
|
Use of Low Pressure Devices to Reduce Surge
Like
the use of a restriction orifice this approach sounds like a reasonable way
to limit peak flow, but it creates other problems! These devices can be
implemented in several ways:
-
A low pressure device can be used on a cylinder supply as a
regulator/flowgauge. These devices generally operate at from 5 to 9 psi
to achieve the desired surge reduction effect. However MIG (and TIG) gas
supply systems were designed to operate at above 25 psi for a very good
reason; to maintain preset flow even when inevitable
restrictions occur in production. These restrictions occur due to spatter
build-up in the torch nozzle and gas diffuser, bent and twisted torch
cables, debris accumulated in the torch gas passage, etc. Flow
control with these low pressure devices is being set by an orifice in the regulator/flowgauge.
To maintain flow when system restrictions occur the flow control must act as a
critical orifice. To do that the pressure up-stream of the flow
restriction orifice must
be greater than 2 times the downstream pressures. Both measured as
�absolute pressure, i.e. gauge pressure plus 14.7 psi. Typical pressure
needed at the feeder to flow the required MIG gas is about 5 psi or about
20 psi absolute. Therefore the pressure upstream of the orifice must be
about 40 psi absolute or 25 psi gauge (40 � 15.) That is what the minimum
pressure in most regulator/flowmeters has been 25 psi or greater since the MIG
process was introduced in the 1950�s! See
�Automatic Flow Compensation" for a full explanation of this
phenomena.
-
The second way these low pressure devices are used is to
place them at the feeder. This not only has the problem outlined in
the previous paragraph but also provides insufficient gas at the weld start to properly
purge the weld start area of gas. Stauffer in his 1982 patent clearly
defined this need, See what Stauffer
said. The following is an example of
tests run with a Conventional Regulator Flowmeter using a 25 psi regulator
and for comparison a commercial Low Pressure
Device that uses a low pressure regulator
mounted at the feeder. In this case to flow the desired preset gas
of 31 CFH
required a regulator setting at 9 psi (defined by
installing a test pressure gauge).
This
particular device incorporates a pressure gauge (upstream of an orifice) calibrated to read
flow.
Both systems were set to flow 31 CFH and then no adjustments were made as
if they were locked (see data in green). Torch restrictions were
then varied to simulate the
addition and elimination of spatter in the nozzle and gas diffuser.
Flow Control System |
< Typical
Production Restriction Range; psi
> |
3 psi |
4 psi |
5 psi |
6 psi |
7 psi |
8 psi |
Conventional = 25 psi |
31 CFH |
31 CFH |
31 CFH |
31 CFH |
31 CFH |
31 CFH |
Low Pressure; 9 psi |
37 CFH |
34 CFH |
31 CFH |
27 CFH |
23 CFH |
16 CFH |
Note the Conventional
Regulator Flowmeter
maintained the preset 31 CFH without
interaction by the welder. However with the Low
Pressure
Device
flow varied from a high of 37 CFH to a low of 16 CFH! While this
occurred the flow calibrated pressure gauge continued to read 31 CFH since it was really
only reading pressure and gives no indication to the welder, welding foreman
or welding engineer that flows change! Only measuring at the torch is
the flow change detectable.
This testimonial
is from a welding engineer at an automotive OEM who removed and discarder 32 of
these low pressure systems that mounted at their wire feeders after he
discovered the inaccuracy�s of controlling flow with this approach.:
�A
welding engineer at a major automotive sub supplier reports that after
purchasing and using 32 low pressure gas saving devices that mounted at
their wire feeders he had to discard all of them! He reported two problems:
-
Lack of
sufficient extra gas at the start made inferior starts and
-
Large flow
variations from preset levels were evident when he would check flow at the
torch. He stated; "Even if the flow was blocked, the flow
calibrated pressure gauge supplied with these devices had the same preset
reading!"
Want More Details About "Automatic Flow
Compensation?
|
|